Product Overview
Automate Mattress Packaging For Foam, Pocket Coil, & Latex Mattresses
Manufacturers install the compression packaging machine in their facility when they're looking to automate the packaging process, reduce shipping costs per unit, or create an ideal package for direct-to-consumer and retail markets. It features multiple packaging options such as autobag, compress and roll, or compress, fold, and roll.
C³'s Package-First Methodology
At C³, we adopt a product-first methodology when customers look to install a compression machine. What is it made of? What kind of package do you want to produce? How will it be transported? How long will it be packaged? What do your customers expect?
We work with clients to calculate ideal packaging options for their products. Then we select the best machine for the job. Here are examples of ideal packages created with this machine.
King Pocket Coil Hybrid Mattress, 4-Layer
This king-sized pocket coil hybrid mattress has four layers. It is a hybrid of foam layers and a pocket coil layer. When packaged with the CF1396, it reaches the following dimensions.
Final Package Dimensions:
Diameter: 18.5 in (470 mm)
Height: 40 in (1016 mm)
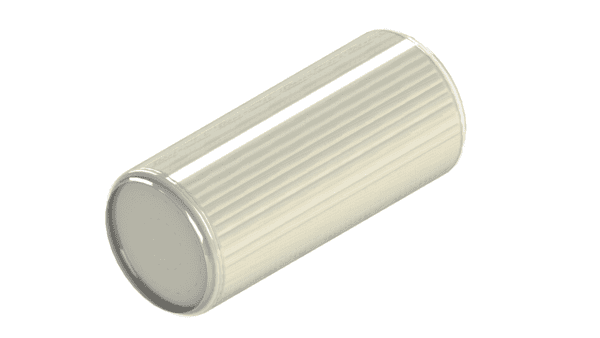
Queen Foam Mattress Rolled To Width
This queen foam mattress has four layers of foam, visco and conventional. It is packaged with the CF1396 without the use of the fold section and reaches the following dimensions.
Final Package Dimensions:
Diameter: 16.5 in (419 mm)
Height: 80 in (2032 mm)
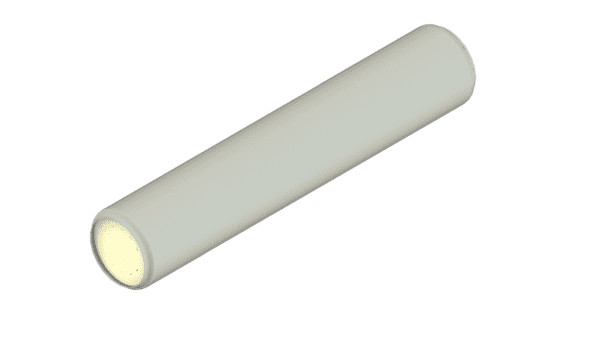
King Foam Mattress, 4-Layer
This king foam mattress has four layers. Made of visco and conventional foam, it reaches similar dimensions as a queen sized mattress of a similar build. This allows you to use similar packaging for differing mattress sizes.
Final Package Dimensions:
Diameter: 17 in (432 mm)
Height: 40 in (1016 mm)
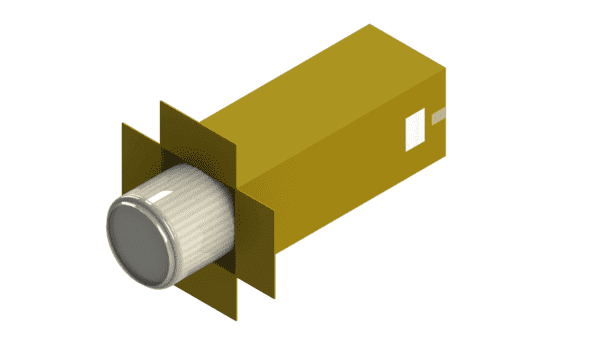
Auto-Bagged Queen Mattress
This mattress only needs to be auto-bagged, so it passes through the CF1396 without the use of the fold or roll cage section. It reaches these dimensions wrapped with polyethylene film.
Final Package Dimensions:
Length: 60 in (432 mm)
Height: 10 in (254 mm)
Width: 80 in (2032 mm)
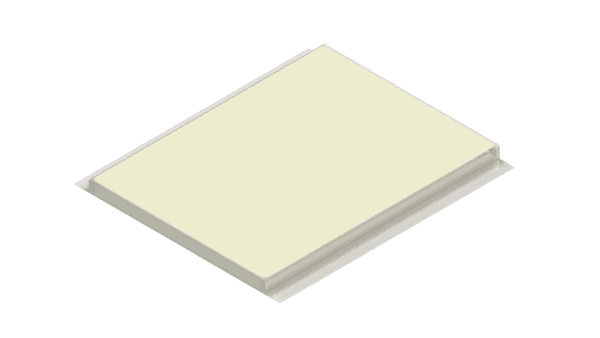
Compression Machine Features
Compress
The tamp press guarantees consistent compression with a four-corner control design that limits product distortion and protects the machine.
Seal
C³-engineered heat seal bars seal poly film to lock in the package's compression.
Fold
The compression packaging machine's fold section folds the product in half before entering the roll cage creating a smaller package height.
Roll
C³'s roll cage rolls products to a set dimension, allowing the product to naturally expand to final specs instead of by force.
More Variability In The Same Machine
When C³ sets out to engineer a machine, we work to create a standard design that delivers the most-used functionality first. Then, we offer additional components that help you scale your equipment to suit your needs. These add ons are modular and can be added at any time to your compression packaging system.
- Boxline
- Second Cage
- Variable Cage
- Traversing Stretch
- Quality Testing
- Trifold Module
- Paper Wrap Module
- CF Rotate
Boxline Add-on
The boxline is an ergonomic addition to lift final rolled packages to waist height. Once here, the product is shuttled on a table where an operator can assist it into a box. Without the boxline, the product drops from the cage and rolls to a stop. The boxline brings the product to a safe height for handling and helps the operator quickly box and stack the finished product.
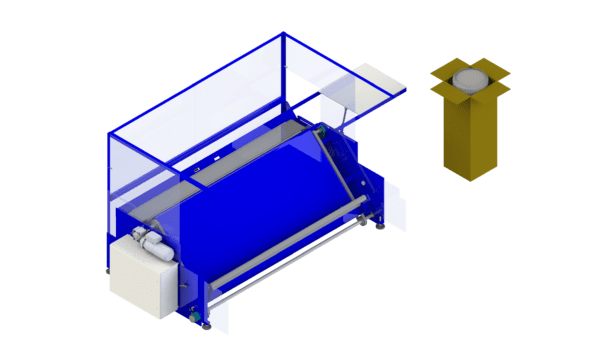
Second Roll Cage Addition: RC1434
The second roll cage takes the level of compression one step further. The product is compressed and rolled to a larger diameter, then rolled again into a tight, small package. This package is nearly 50% smaller than the standard. For bigger benefits, use paper wrap to replace stretch wrap for a more environmentally friendly option.
Example 3-Layer King Mattress:
Standard Package: 15 in x 15 in x 44 in (381 mm x 381 mm x 1118 mm)
Secondary Cage Package: 23 in x 15 in x 15 in (584 mm x 381 mm x 381 mm)
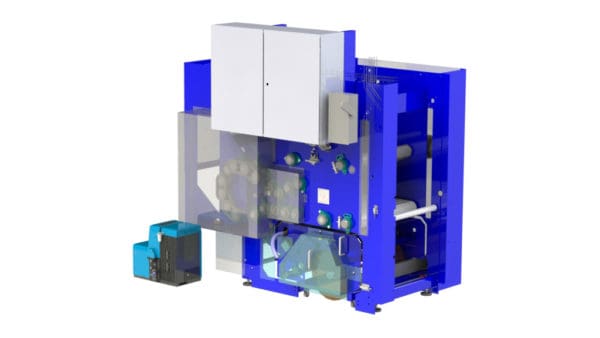
Variable Roll Cage for CF1396: CF9500-VC
This option replaces the standard roll cage on the compression folding machine with a cage that provides greater diameter ranges for products. This allows facilities to package products with varying diameters in one machine. This roll cage is ideal for operations that package many different SKUs with recipes that require varied packaging for each.
Standard Roll Cage Dimensions: 13.6 – 16.3 in (345 mm – 414 mm)
Variable Roll Cage Dimensions: 7.5 – 18.5 in (190 mm – 469 mm)
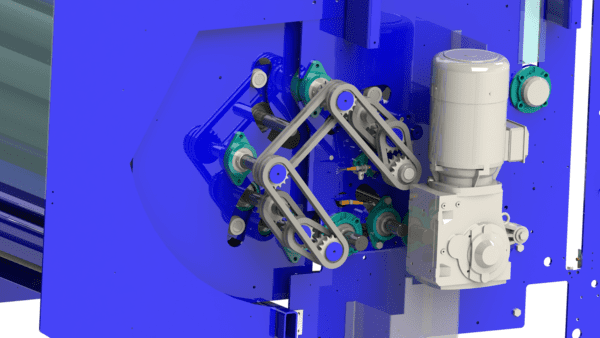
Traversing Stretch Option
This option comes standard on all new compression folding machines, but can be purchased as an upgrade on earlier versions of this machine.
If you are packaging a smaller product, you use a smaller sized roll (50 inch roll for a 40 inch product height). To package a longer product, you need to switch out your roll for a larger size (like a 100 inch roll for an 80 inch product height). With the traversing stretch wrap option, the cart moves the stretch film side to side to cover products of many sizes without having to change film rolls. This is a great way to reduce the number of film sizes you need.
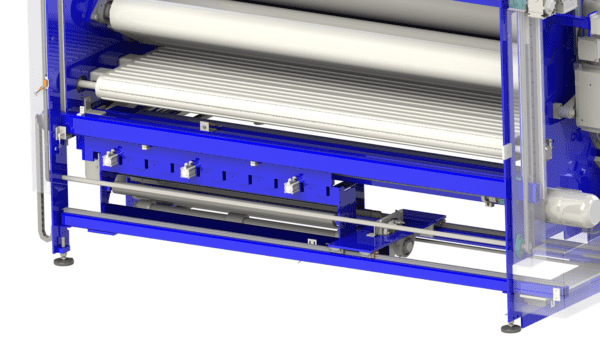
Force Deflection QA System: FD1000
The Force Deflection QA system prevents faulty product from being packaged and shipped off to customers. The machine tests a finished mattress at two set points of compression and determines if it passes or fails according to your set tolerances. The system sits in-line with the packaging machine and takes only 25 seconds as to not bottleneck your line. Common issues detected by the FD1000 include cover tightness, lot-specific quality issues, and incorrectly built mattresses.
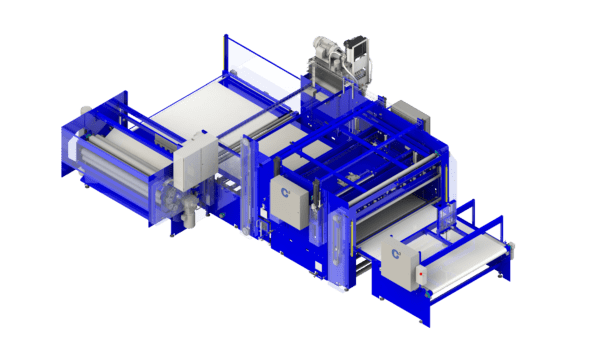
Trifold Module
The C3 trifold add-on increases pallet density and improves logistics costs by folding a mattress in thirds rather than half. With a final cylindrical package size of 16×30 inches, the trifold allows more mattresses to fit on trucks and retail shelves, which reduces your shipping and inventory costs.
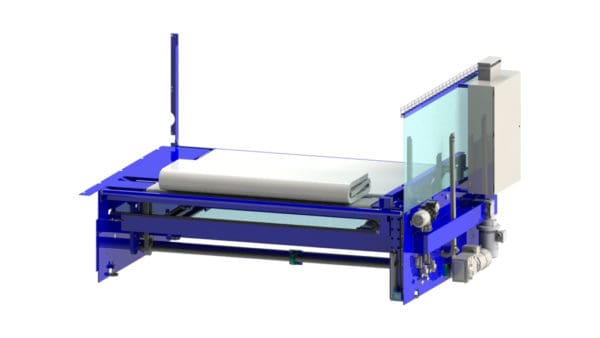
Paper Wrap Module
Replace stretch wrap with paper wrap as the final packaging material for a more sustainable option. The paper wrap module add-on can be easily integrated into existing C3 compress and fold machinery. Impress your consumers and decrease your plastic usage with recyclable paper.
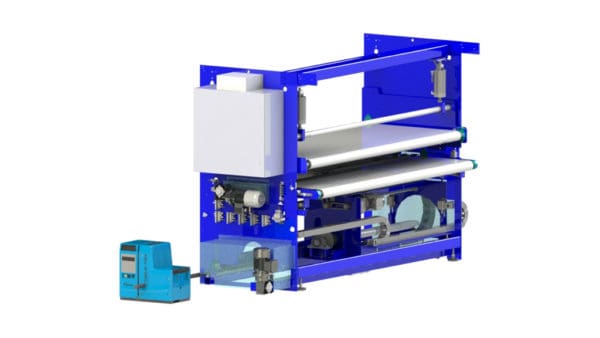
CF Rotate
The C3 rotate add-on allows the mattress to enter the machine with its longest side running parallel to the width of the machine. Less poly film is used to cover the mattress during compression, saving you time and materials. The rotate is located after the compression unit and pivots the mattress 90 degrees to continue on the tamp as usual.
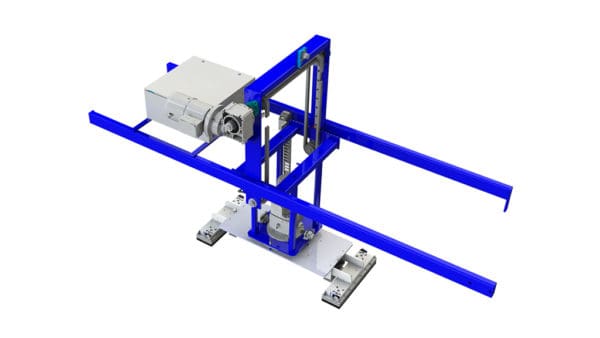
Get More Out Of The Compression Folding System
C³'s modular machines allow you to easily scale your equipment to get even more out of their capabilities. See how you can scale your CF1396.
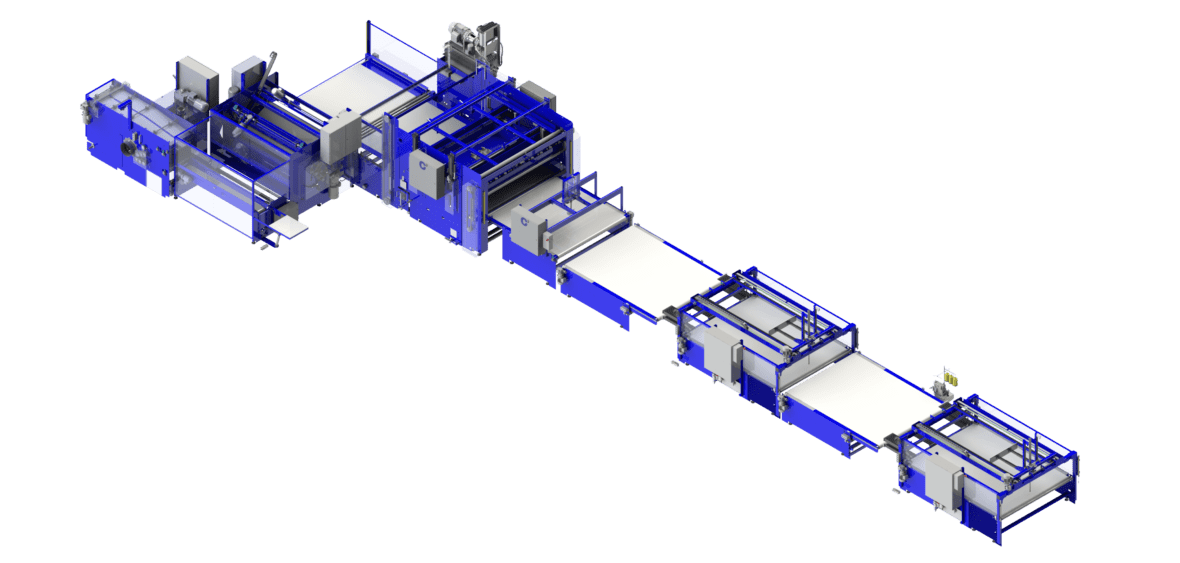
Maximize Throughput
When the compression folding system is part of a manufacturing line, you maximize its 120+ packages per hour throughput by keeping work in progress through to packaging or taking advantage of accumulation.
Increase Packaging Options
Packaging add-ons scale the capacity of your machine by providing more package variability in the same machine footprint.
Guarantee Quality Product
Adding a force deflection system checks each unit for quality before packaging and sending to customers. In line testing keeps a full manufacturing line moving without disruption.
Ready to Automate Your Process?
Frequently Asked Questions
Most foam and latex mattresses have the capacity to be compression packaged. Pocket coil mattresses without wire rims also can be compression packaged. Every product is different – the best way to know is to contact C³ and schedule product to be sent to our facility for testing.
The compression packaging machine uses two types of film. The press section utilizes a polyethylene film that locks the compression in place. At the roll cage, a stretch film is used to hold the roll dimensions and create the final package. Both films can be purchased through C³.