Product Overview
Flexible, Accurate Placement, & Ergonomics In One Lamination System
This lamination system provides a balanced use of automation and operator involvement at the build section. The machine handles glue application, lifting, and placement of the layers. Now operators simply need to make easy waist-height adjustments before sending it off to the tamp press. It is an ergonomically-friendly design with fast throughput.
Efficient Automation with C³ Lamination
The LCN1350 takes the best tools of automation and pairs them with the quick adjustments only an operator can do. It protects your builds from error and your operators from injury.
Every drop of glue should be used to adhere the layers of your build, not create a mess on your floor or on your products. C³’s lamination works towards efficient use of glue to save you money in consumables and in overall production efficiency and quality.
Example Lamination Build
For a queen hybrid mattress build.
Base Layer: 1 in foam plate
Rails: Rails applied to base layer using hot melt
Pocketed Coils: Hot melt applied to foam encasement, coils merged into foam encasement then hot melt is applied to coils.
Mid Layer: 1 in layer roll coated with water based adhesive
Top Layer: 1 in layer merged onto mattress as final layer
Using gap control, the rollers will meet the foam at the right height to ensure each layer reaches the necessary glue coat weight. This prevents too much or too little glue application.
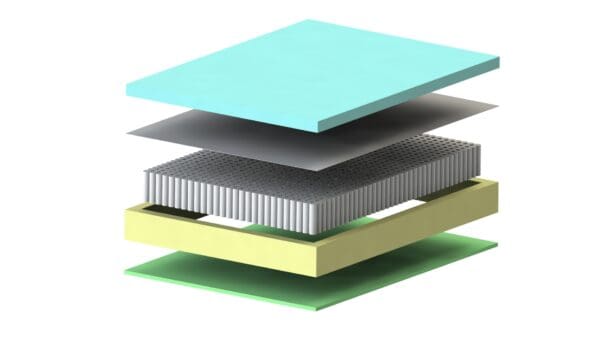
How The Lamination System Works
Hot Melt Application
C³ comb tips apply hot melt evenly and with accurate glue placement.
Water Based Application
C³ application rollers apply glue efficiently at a perfect coat weight with automated gap control.
Place
Product is placed within 1-inch of accuracy. Operators can man the build table to manually adjust layers if needed.
Merge
Merge table eliminates heavy lifting of coils into the foam encasement.
Adjust
This unique design allows operators to make last-minute tweaks to the build without any lifting.
Tamp Press
The tamp press secures the glue’s bond and speeds cure time.
Take Advantage of The Lamination Machine's Biggest Automation Benefits
Because of its efficiency, throughput on this lamination system is rapid-fire. Here's how manufacturers amp up their machine to take full advantage of its features.

Fast Throughput
Automating with the LCN1350 brings the fast machine throughput to your production.
Room For Adjustments
The build table on the lamination system allows for operators to make small adjustments to a build or introduce a pocket coil or special layers to the line, allowing for variability.
No Heavy Lifting
With the LCN1350's merge table, the machine places layers onto a laminate build so there's no lifting involved in production.
Ready To Automate Your Production?
Frequently Asked Questions
- Foam or latex layers
- Pocketed coil layers
- Convoluted or contoured layers
- Scrim material and most nonwovens
Operators using the LCN1350 never lift at the build station, only perform small finger adjustments. The placement is within a 1-inch accuracy, so adjustments are minimal. This allows for improved ergonomics of your facility.