C³'s Phased Approach To System Design
Understand Your Needs Today
Most clients start automation adoption with a section of production such as lamination or packaging. C³ engineers can help you determine your focus for the biggest impact today.
Evaluate Your Production Goals
What do you manufacture? How much do you plan to grow? What's your biggest bottleneck? We'll review this and more when planning for your production line.
Structure Phase 1
After understanding what you're manufacturing today and your future goals, we'll then structure a plan for Phase 1 installation.
Installation & Training
Installing new machinery on your floor has a learning curve. C³ provides onsite install and training for your team at each phase.
Plan For Phase 2 & Beyond
Once you're up and running with the first phase of installation, we discuss where the biggest impact will be to engineer your second phase and beyond.
Ongoing Support
C³ is here every step of the way. For the big dreams of Phase 1, to the hiccups that might occur in your plans along the way. We scale with you and adapt to changes for the longevity of our machines.
Ready To Schedule A Consultation?

Automate Lamination And Install A Packaging Machine
This line scales a stand-alone lamination system with a stand-alone packaging machine. It brings assembly in to create a straight pass-through manufacturing line. Automation benefits are at the pallet management section, feeding layers of foam by a recipe for the current SKU, and with the LCN1250. Ergonomics improve for the assembly section with the aid of the pushers units to add fire socks and covers.
This system’s throughput is determined by the speed of the assembly section and the operators’ ability to put covers on efficiently. This line assumes layers are coming in pre-cut and within tolerance with no trim needed after lamination.
Stats When Manufacturing An All-Foam 3-Layer Mattress
*Based on one 8-hour shift at 70% uptime
Machines & Add-Ons To Create Phase 1
Ready To Schedule A Consultation?
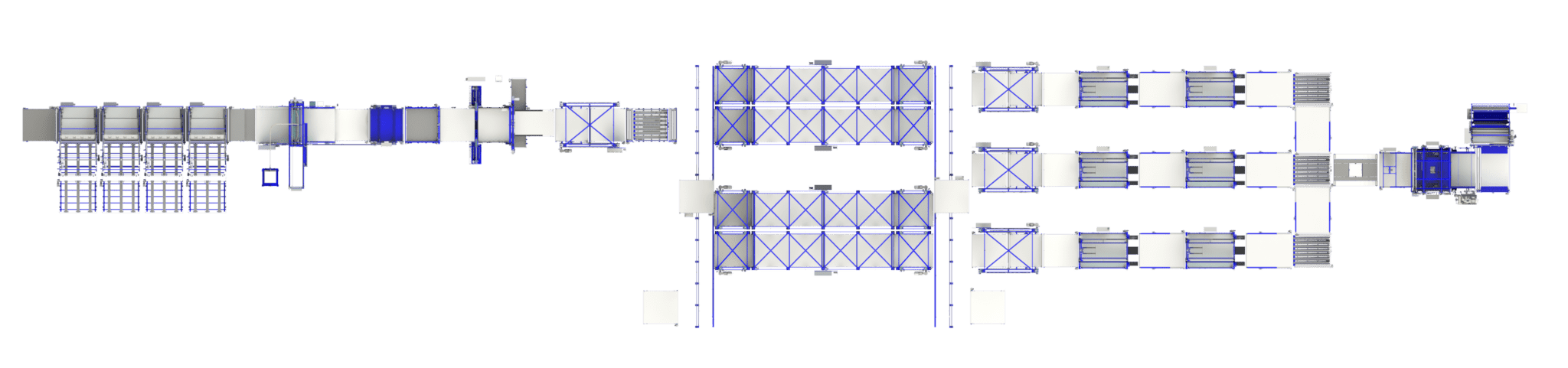
Ramp Up Assembly And Add Storage For Accumulation
This line scales the Phase 1 line by adding a trim section, storage racking, and two more assembly lines. Now you can produce 60% more product and yield more product per operator.
Since assembly was the bottleneck in Phase 1, we triple it here so we can make the most of the throughput for the lamination and packaging systems. This allows product to be made up to 60% faster per unit.
The next phase will be driven by the need to scale the lamination section so you can double production volume.
Stats When Manufacturing An All-Foam 3-Layer Mattress
*Based on one 8-hour shift at 70% uptime
Machines & Add-Ons To Create Phase 2
Ready To Schedule A Consultation?
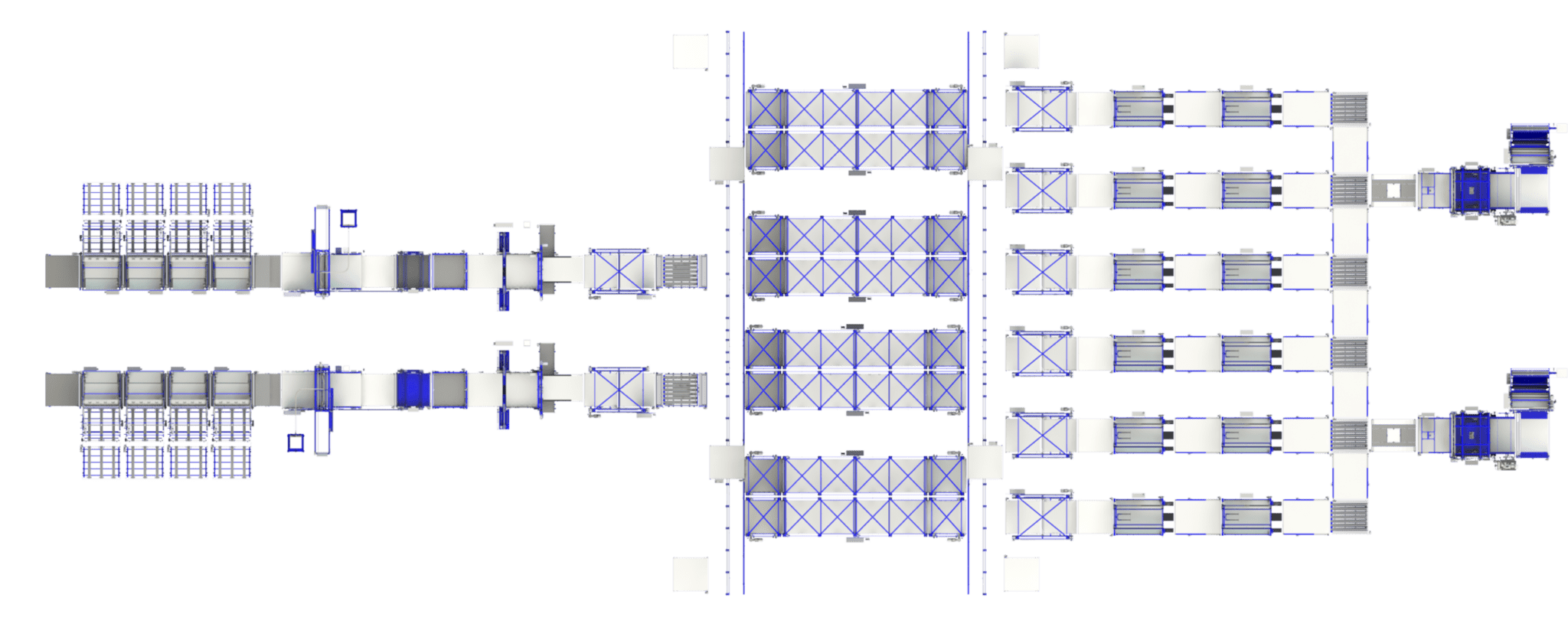
Become An Industry Leader
Phase three of this example bedding line doubles phase two into a full-scale automated bedding production. Now you’re manufacturing twice as much product with utmost efficiency.
Full production automation requires 32 operators, 24 of which are dedicated to the labor-necessary assembly section. Four additional operators will run both lamination lines at the start of production, and four others will finish product at the packaging station.
All in all, a system like this can produce almost 332,000 units per year.
Stats When Manufacturing An All-Foam 3-Layer Mattress
*Based on one 8-hour shift at 70% uptime
Machines & Add-Ons To Create Phase 3
Ready To Schedule A Consultation?
Frequently Asked Questions
Systems can get complicated fast. Multiple vendors with different software or approaches to automation can quickly complicate installation. To keep things streamlined – from install, training, maintenance, and service – it’s best to work with one vendor who will understand the whole line.
Everyone. Whether you’re investing in a stand-alone roll cage or looking to add destacking units to your lamination line, everyone should consider how their business plans to grow after installing new machinery.
Phase 1 usually entails installation of the main machinery needed to keep production running – things like a lamination or packaging machine. When we install these first, your team can learn the equipment and produce product immediately. Then by Phase 2, your teams are familiar with C³ machinery and how it operates, which makes scaling from there much easier.