Product Overview
Laminate Foam, Latex, & Pocket Coil Products With Roll Application
Whatever way you manufacture mattresses, this machine is capable of a variety of foam types, mattress builds, and glue needs. With the same robust design as other C³ lamination equipment, this machine capitalizes on roll application efficiency while preserving needed operator involvement.
Maximize Adhesive Efficiency with C³ Lamination
Often, the LCN1000 system is installed to replace spray application processes. When installed, the accuracy of glue dispensing and adhesion immediately improves.
Every drop of glue should be used to adhere the layers of your build, not create a mess on your floor or of your products. C³’s lamination works towards efficient use of glue to save you money in consumables and in overall production efficiency and quality.
Example Lamination Recipe
For a standard queen, 3-layer foam mattress, we impart the following example recipe.
Glue per layer: 6 g/ft2
Tamp Press Recipe: 25% compression with a 1 second dwell; 50% compression with a 1 second dwell
Total Throughput: 45 seconds
Using gap control, the rollers will meet the foam at the right height to ensure each layer reaches the necessary glue coat weight. This prevents too much or too little glue application.
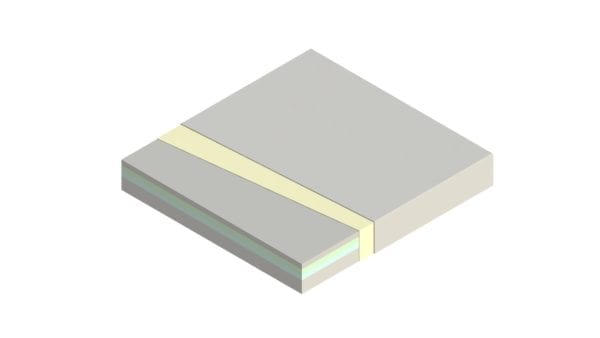
Semi-Automated Lamination Machine Features
Product Infeed
The machine measures each raw material as it enters the system and adjusts the rollers to reach the desired glue coat weight.
Roller Application of Glue
The rollers adjust for straight-cut, contoured, or convoluted foam or latex layers. The rollers slightly penetrate the foam to ensure optimal glue coat depth.
Assembly
Two operators work at the assembly station, where they take glued layers of foam and stack them to make the build. They can also intervene to glue foam rails.
Tamp Press
Once the laminate is built it conveys to the tamp press. Here, the laminate is compressed multiple times to help cure the glue.
Get More From Your C³ Semi-Automated Lamination System
Modular machinery allows you to take advantage of automation where you need it most. Here's how you could scale your LCN1000 system into production.
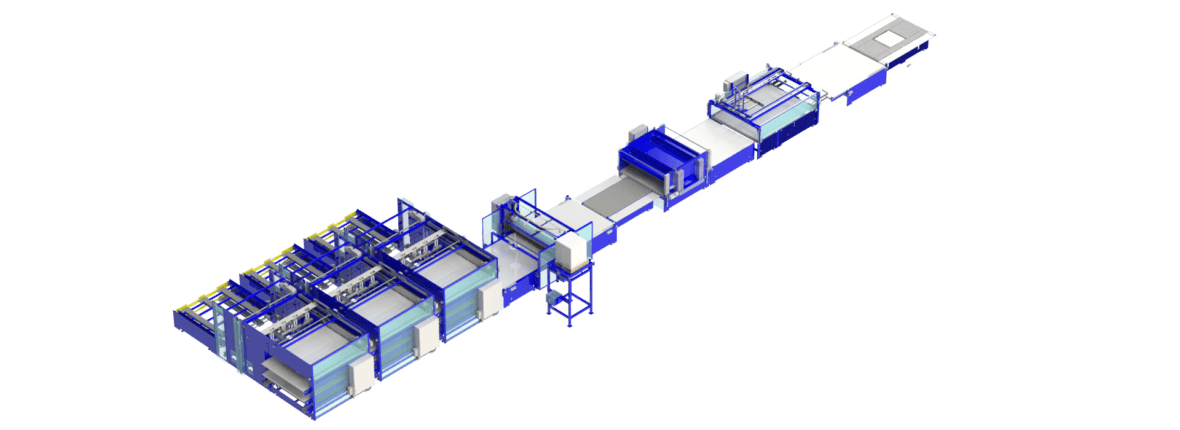
Automate The Infeed
Adding destacking units to the front of the system automates the material handling at the start of your line.
Continue Straight Into Packaging
With pushing units and conveyors, you can connect this lamination line right to packaging. You'll never lose track of product again.
Versatile Build Section
Since the LCN1000 is semi-automated, it leaves room at the build table for operators to build encasements or make adjustments.
Ready To Automate Your Lamination Process?
Frequently Asked Questions
Most facilities operate this machine with 2-3 operators. There is also a “one-man mode” that adjusts the process to allow for one operator to run the machine and build product.
Yes, many customers use the LCN1000 with hot melt glue. For this, you’d opt for a hot melt addition to the system as shown. You can also have the hot melt add-on completely replace the application roller section if you don’t need it!
- Foam or latex layers
- Pocketed coil layers
- Convoluted or contoured layers
- Foam rails
- Scrim material and most nonwovens