Not much has changed in the last decade for laminating mattresses. Production speeds have been limited by two major factors: the time required to manually stack plates, and the time needed for the bonds to cure. It’s common to see production rates of one bed per minute – sometimes as slow as one bed every two minutes.
Lamination lines across the industry seem to be running slower to appease operators’ capabilities and glue’s curing properties. The solutions the industry is seeing relate to adding drying units or replacing glue altogether, yet no one seems to be looking at the greater production line.
How can we make the operator’s job more efficient? What glue has the best properties for fast cure times? What functionality is already in our machinery that we can take advantage of?
Joe, our CEO, wanted to seek solutions to these production woes. “You have to focus on production or you aren’t profitable,” he says. “We’ve turned things around and looked at how to achieve production, then found an ergonomic solution to improve the lamination process.”
Grant, our lead mechanical engineer for lamination, led the research and development of upgrading the lamination system to make production more efficient. Hear more from Grant and Joe about what went into creating our newest lamination machine, the LCN1250, and how it solves these production setbacks:
Improving Workplace Efficiency
Manually assembling the layers of a bed is strenuous, and our engineers knew this process needed an overhaul. “We looked at lamination from the operators’ standpoint and how we could alleviate the lifting and placing,” Joe explains. “The first thing we did was take the weight away by automatically stacking the plates.” To do this, we developed a merge section: the build station conveyor retracts under the lamination conveyor, then both move forward together as the next plate comes down, thus stacking and merging them to make the laminate.
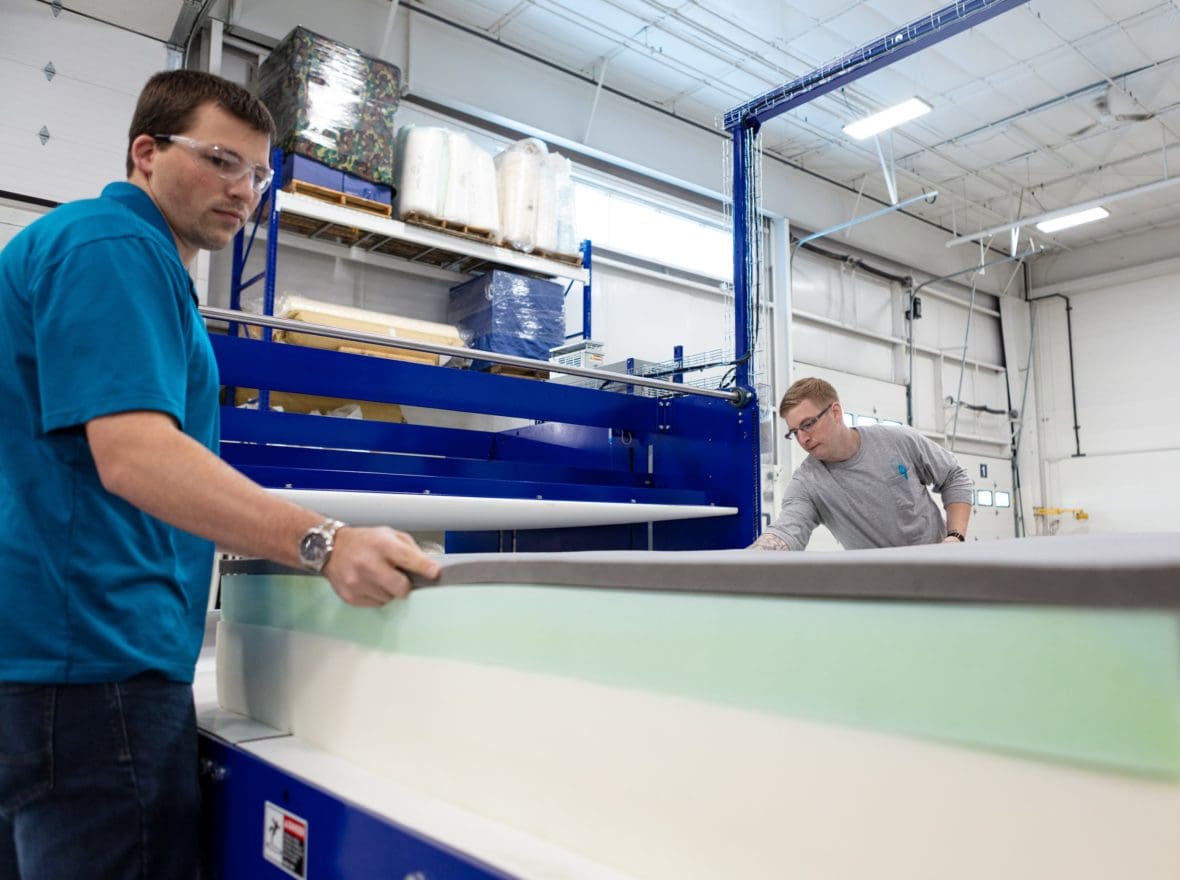
As it turns out, this method of auto-stacking the plates was all-around more efficient. It not only alleviated the operators’ repetitive motions, it also greatly reduced the time required to finish a build. This merge station concept means the LCN1250 can run at a roller speed of 200 ft/min and a continuous passthrough rate of 10-12 plates per minute, or 2-3 beds/min. When compared to the 30 ft/min run speed for most acrylic glue systems, that’s nearly seven times faster.
Achieving Accurate Placement
Manufacturers often prefer having their operators manually place layers to build a laminate because they do so more precisely than the existing machine-based methods. Those operators also become a part of quality control, making quick adjustments to verify the build is ready to move on before those layers are permanently bonded. Our engineers looked for a way to hone our automated stacking ability, while still leaving any final quality adjustments to the expertise of the lamination operators.
This led to the development of the pivot conveyor. As each freshly laminated plate comes down the line, the end of the pivot conveyor lowers to 2-inches above the build. This feature allows for more control of the stacking process. Additional timing adjustments can be made on the HMI to further refine this.
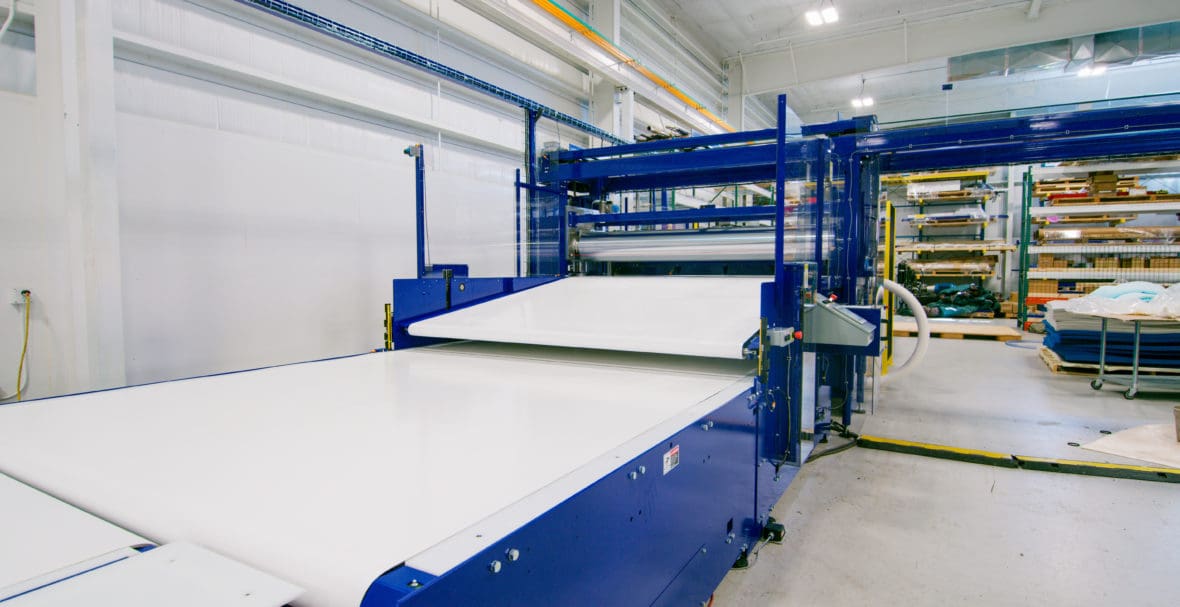
By designing a machine that not only auto-stacks the plates but does so with +/- 1-inch accuracy, any last-minute adjustments are now made with only quick wrist movements at waist-height before sending the build on to the tamp.
Controlling Glue Application
Many mattress manufacturers feel their production speed is limited because the glue needs time to cure, particularly with the use of acrylic glue. This process provides a secure bond, but at what cost?
As Joe said earlier, the goal with this line was to shift our focus to increasing throughput, then find the right glue. While the LCN1250 supports multiple adhesive options, we’ve determined that using synthetic latex glue allows it to maintain its speed while still creating a secure bond. It requires fewer grams per square meter to achieve the same bond as acrylic glue, without the IR heater add-on.
You can further monitor your glue consumption with our automated gap control, which adjusts the roller gap automatically for each layer. Each layer gets only the glue it needs, which reduces unnecessary moisture. Controlling glue usage by applying only what you need not only means glue cost savings, it also means reduced curing times and the ability to move on to packaging faster.
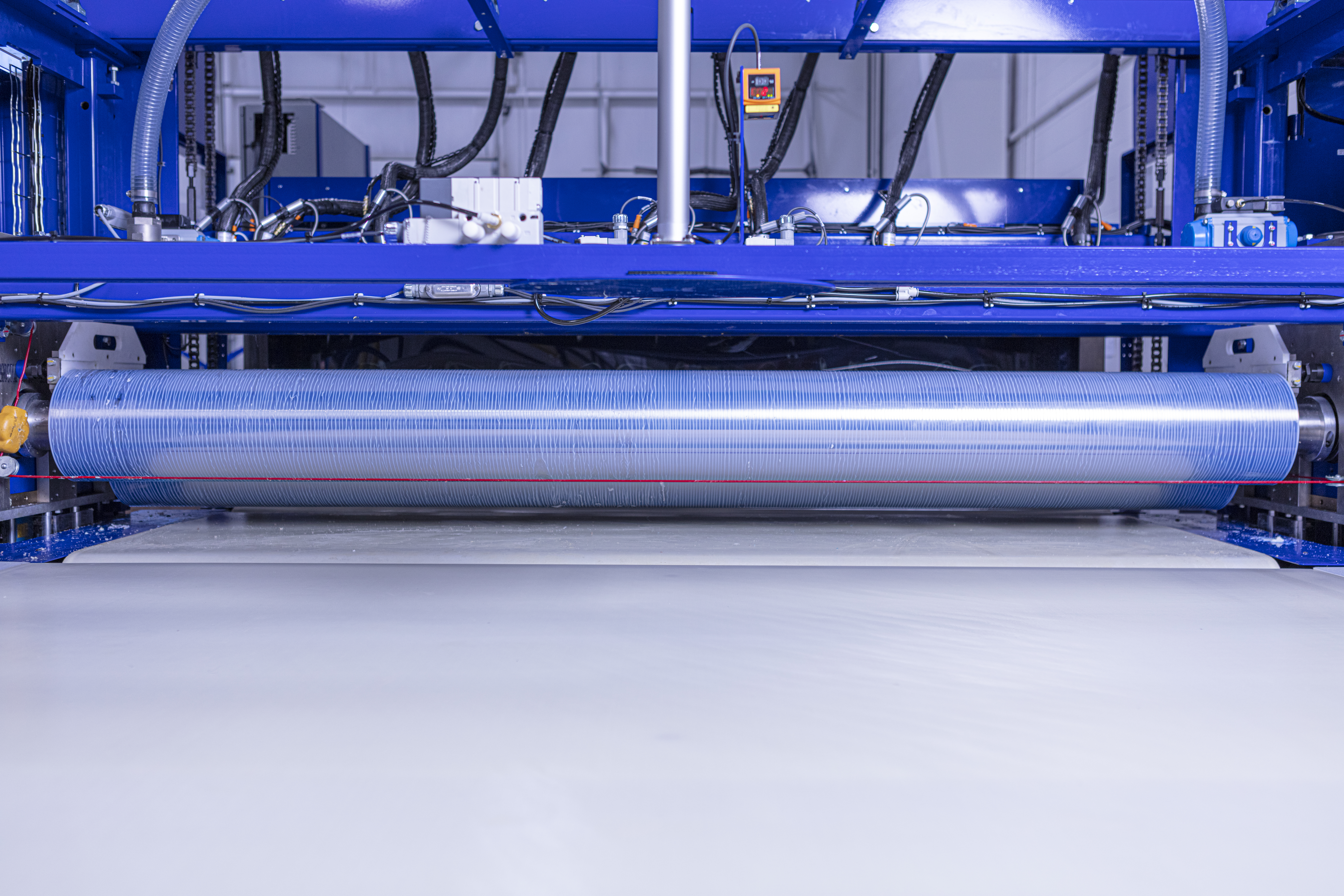
By incorporating existing glue consumption features like our automated gap control with these new innovations for fast and accurate stacking, the LCN1250 answers what our lamination team set out to do. The result is an efficient machine that incorporates all the accuracy benefits of operator involvement while taking away the delays and strains that come with manual placement.