C³’s newest lamination system, the LCN1250, sets a new standard for mattress lamination. It brings the best of C³’s gap control technology, precision roll coaters, and speed to one machine. It capitalizes on automation technology paired with the operators’ final quality adjustments.
Watch the video to see how this machine and its operators work seamlessly together to increase throughput and improve overall efficiency.
The following components of this machine allow it to trump any other lamination system on the market in application accuracy, speed, and safety.
New Merge & Build Section
The merge and build section sets the LCN1250 apart from other lamination systems. Here, the conveyors place each layer automatically to build the mattress without any lifting by operators. Because the machine handles each layer rather than operators, throughput increases. This allows for doubling the speed of the system as compared with the industry average*.
Here’s how it works: The first layer passes under the rollers and receives an application of glue. As it exits the rollers, the pivot conveyor lowers to gently place the layer onto the build station conveyor. The build conveyor then retracts the base layer under the pivot conveyor. When the next layer advances, the pivot conveyor lowers again to two inches above the base and both layers move forward in tandem, thus merging them together. This continues until the build is complete.
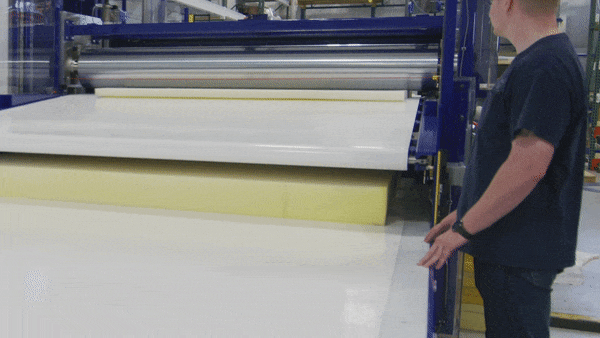
The machine runs as fast as six seconds per layer as a result of this enhancement. Many other roll coat lamination systems run at a max rate of 15 seconds per layer, often limited by the speed at which operators can manually place and adjust layers at the build station.
Because the LCN1250’s merge station stacks layers for operators, it can run at 200 feet per minute. Operators will no longer feel pressure to handle layers fast to maintain throughput. Instead, the pressure is on making sure there’s enough raw material coming in the front of the machine.
Enhanced Ergonomics, Improved Focus
What makes this merge section concept so unique is that it increases speed while alleviating many safety concerns of a lamination operator’s job. Here are the main ways in which the operators’ job is safer on the LCN1250:
1. No Manual Lifting
The merge table eliminates any awkward, heavy lifting from handling glue-covered layers because it stacks them automatically. The merge table also places each layer with +/- 1 inch accuracy, leaving only small, waist height adjustments for the operators. This allows them to focus on quality control and reduces the touchpoints of each operator with the product.
2. No Unsafe Reaching
We designed the LCN1250 to run layers sideways so operators make adjustments from the short sides of the bed. Whether you’re running kings, queens, twins, or any other bed size, the length of each bed size varies far less than the width. By running layers sideways, there is only a 5-9 inch variance across the conveyor. This keeps all adjustments within arms’ reach of the operators and eliminates dangerous leaning that could lead to back strains. It also supports today’s need for social distancing.
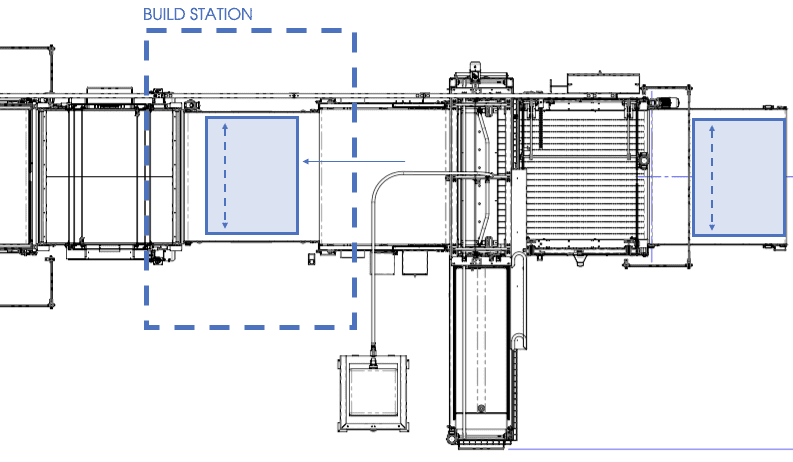
These two differences make an operator’s job far less physically demanding. They can instead focus their energy on sending high-quality laminates down the line rather than on struggling to keep up.
Superior Application Roll Coaters
We equipped the LCN1250 with the same automated gap control used on all of our roll coating systems to help regulate glue consumption. Adjusting the coat weight per layer helps mattress producers save on glue where they were previously over-applying it. In this instance, it would also result in less time required for each laminate to dry.
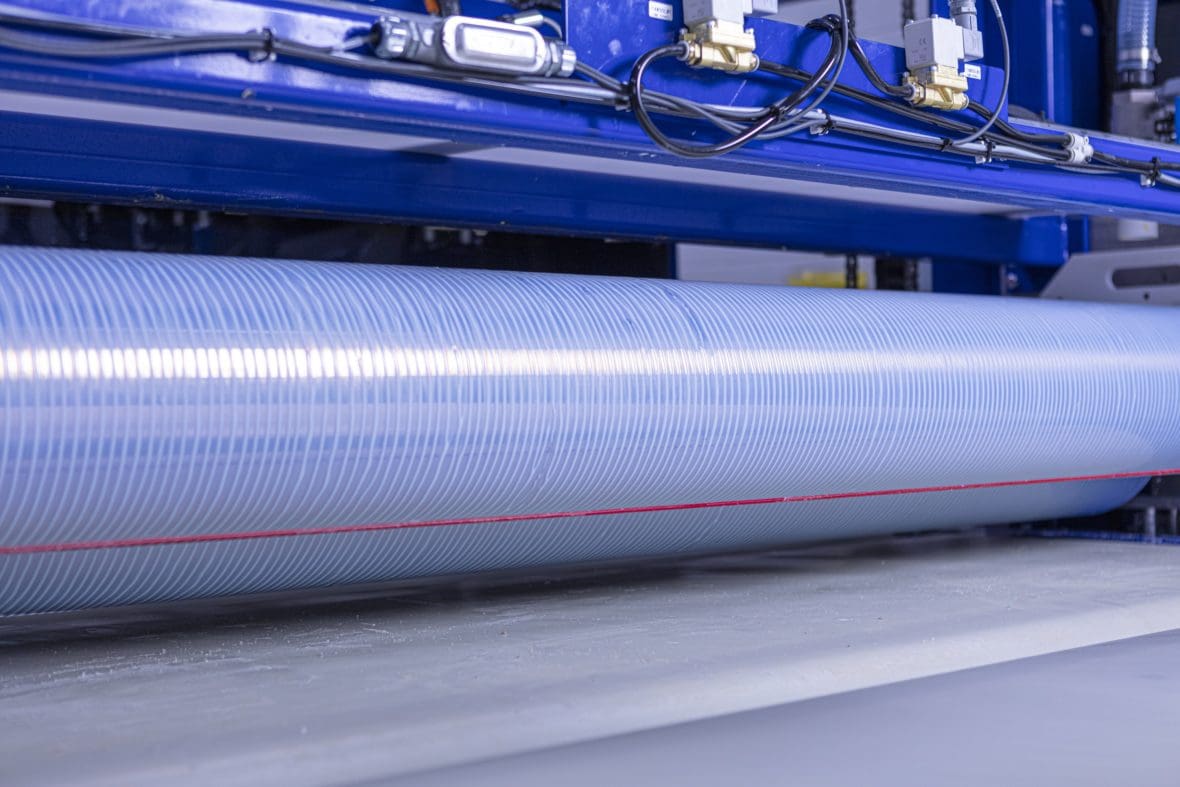
This automated feature adjusts coat weight and depth for each layer in real-time. This allows every application to meet the exact specifications of each layer that passes the rollers. We’ve found that this system works well for improving throughput and adhesion while still allowing manufacturers to control the accuracy of their glue usage.
Tamp Press For Secure Bonds
Once operators have made their final adjustments, they send the laminate on to the tamp press. Here, the tamp uses gentle compression to force air through the laminate, which improves both adhesive penetration and speeds the curing process. The tamp settings are a part of the recipe and customizable to suit throughput and product specifications. Typically, facilities will set the tamp to press as many times as possible before the next laminate is built.
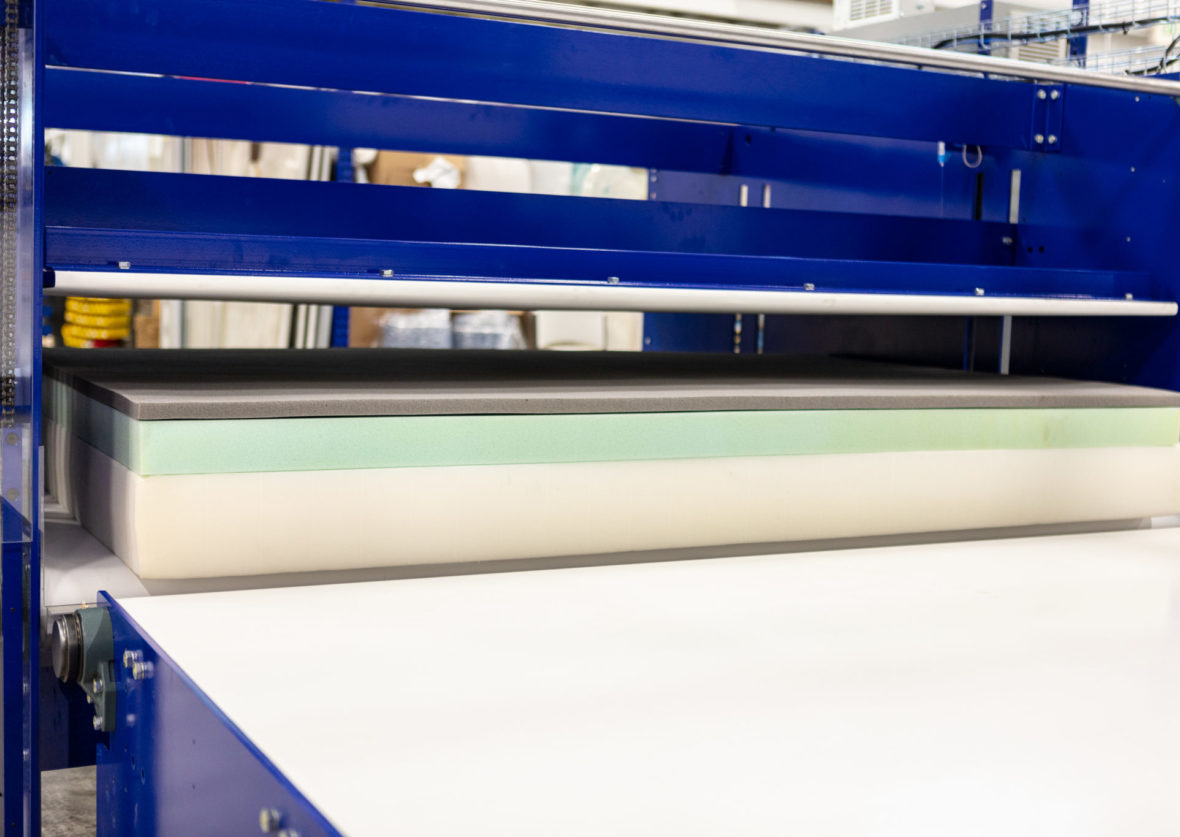
Combining these features into one system solves multiple inefficiencies in ways other lamination lines couldn’t. The conveyors work together to stack layers faster and safer than operators ever could before, allowing them to instead channel their efforts into refining product quality. The roll coaters make the most of your glue usage by always applying the right amount, and the tamp secures the bonds while the next bed is built. Altogether, this opens the door for manufacturers to produce a higher quality product faster than ever before.
Do you have specific questions about how the LCN1250 could work with your products? Contact us to see how the LCN1250 can help make your production leaner and safer.
*Industry average of 15 seconds per layer versus LCN1250’s 6 seconds per layer.