Producing high-quality mattresses depends on creating strong, secure bonds that will last for years. Manufacturers using roll coat systems often use thick coat weights to achieve this because they struggle to obtain consistent coverage across their rollers and throughout a shift. While this certainly leads to secure bonds between layers, it also requires excessive glue consumption and longer drying times.
With C3‘s roll coat system, manufacturers attain consistent adhesive coverage at an optimal glue consumption rate. We’ve designed these rollers to stay balanced and provide predictable, even coats of adhesive, while also programming them to auto-apply the proper coat weights needed per layer. This system allows you to assemble mattresses with high-quality bonds, meter your adhesive usage, and maintain high production rates.
Watch to see what makes our adhesive coating system stand out!
The effectiveness of our roller system is primarily due to its durability and consistency. We designed both the rollers themselves and the automated gap control feature to maintain precision throughout production.
Precision Cut Rollers Designed For Durability
The system consists of two rollers – a nine-inch metering roller and a twelve-inch application roller. The tops of the rollers are aligned, leaving room for the application roller to compress slightly into each foam layer as it passes through underneath. The rollers rotate in opposite directions, and adhesive fills the space between them from above. The rollers’ size creates a large reservoir between them, which helps the adhesive retain necessary moisture when kept full.
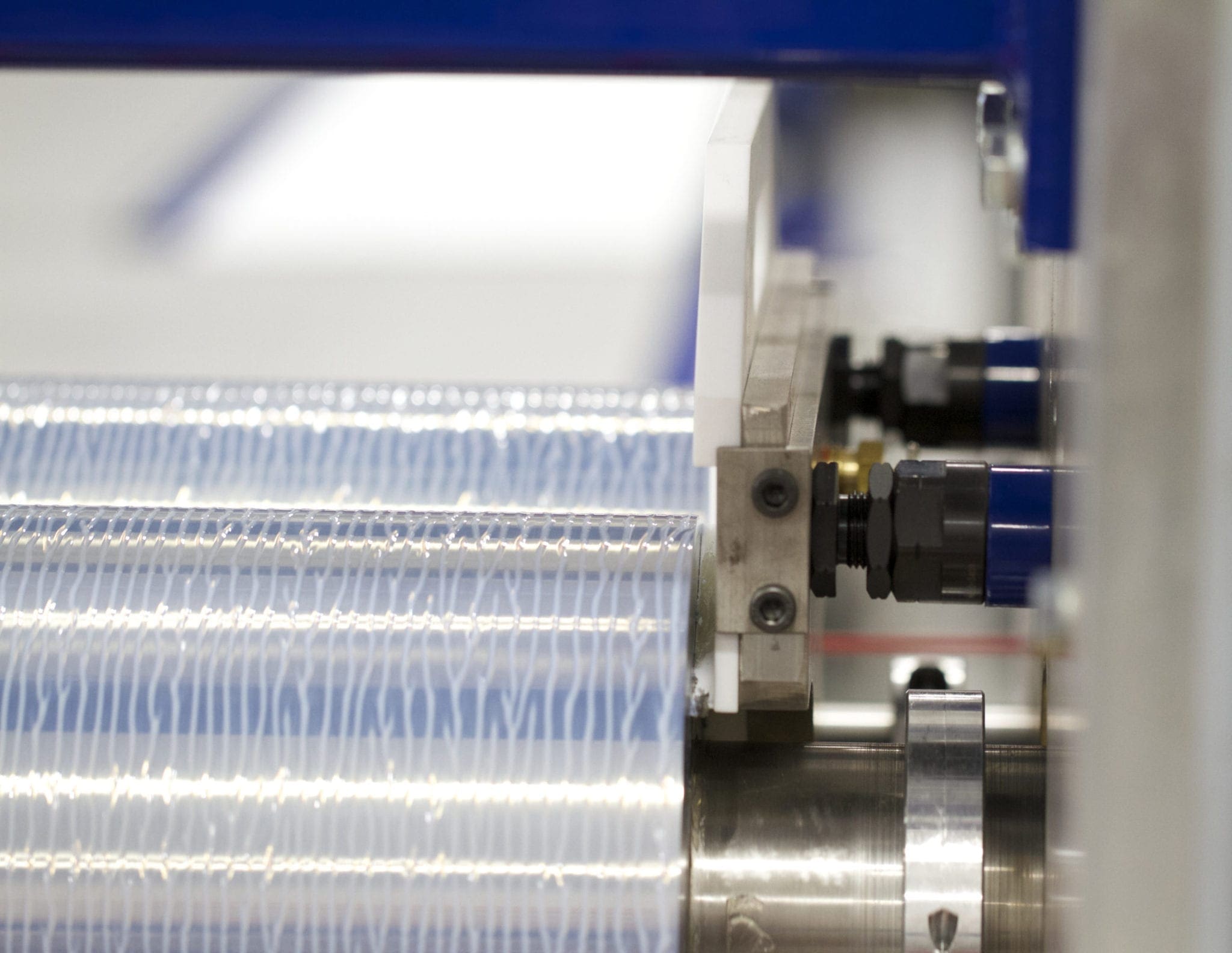
The size of these rollers also contributes to their durability. Each roller has one-inch thick steel walls to prevent any bowing or warping during production. Through R&D, we’ve discovered that thinner-walled rollers are prone to warping, leading to inconsistent adhesive coverage. Both rollers are also nickel-chrome plated to resist scratches, gouges, and other imperfections that could otherwise occur over the rollers’ lifetime through wear and tear.
Calibrate For The Perfect Application, Per Layer
Our automated gap control technology enhances the precision capabilities of these rollers even further. Automated gap control ensures that each layer gets exactly the right amount of adhesive at the proper coat depth for optimal bonds. The rollers are programmable to adjust the gap size and roller height based on the product’s needs.
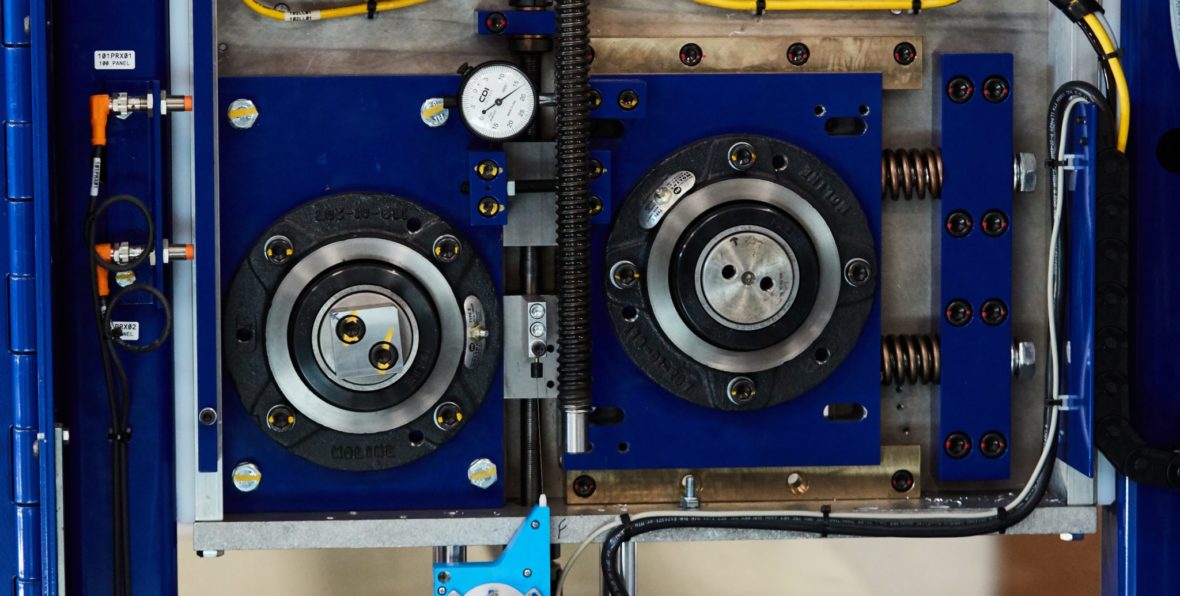
The gap control wedge system allows for precise control when changing the gap on the fly. Each wedge is individually scaled, and separate motors control them to maintain accuracy across the rollers. The wedges then push the metering roller in or out from the application roller to adjust the coat weight. This method accounts for any variances between the two sides when alternating between gap sizes, keeping the rollers aligned from end to end.
Unlock More Production Efficiency With The Right Adhesive
C3 lamination rollers work with a variety of water-based adhesives, but we’ve found that manufacturers attain their highest potential when using synthetic latex. The properties of synthetic latex adhesive allow mattress producers to achieve high-quality bonds with fewer grams per square foot and shorter curing times than acrylic.
First, synthetic latex works particularly well with our roller system because of its ability to withstand shearing, even at very thin gap settings. With the help of the large glue reservoir holding more adhesive (and therefore, more moisture) between the rollers, synthetic latex carries a low risk of clumping during production. Regardless of your water-based adhesive choice, the rollers rotate much slower when idling than at production speeds to further reduce shearing.
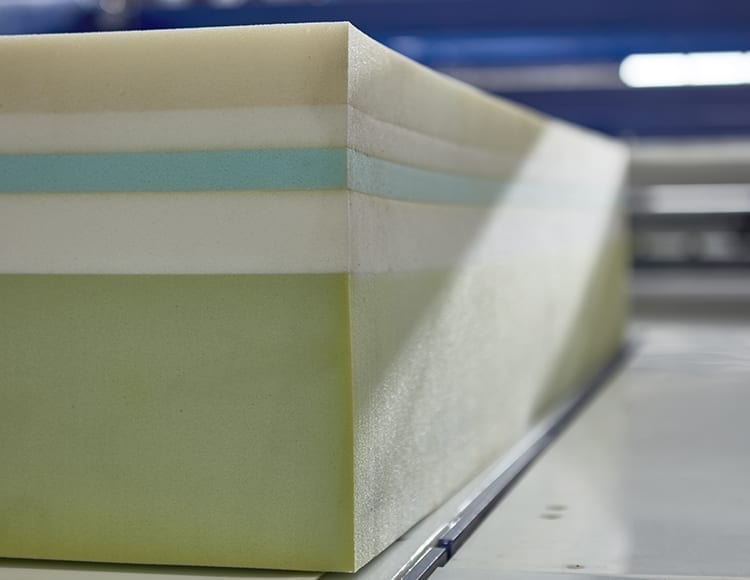
Second, foam requires less synthetic latex adhesive than acrylic adhesive to create a foam-tearing bond. Using synthetic latex with our automated gap control allows you to meter your usage for the best adhesive conservation. 5-6 grams per square meter of synthetic latex typically achieves the same bond as 7-9 grams per square meter of acrylic.
Last, synthetic latex adhesive wipes away easily from the rollers’ nickel-chrome finish. This helps ease cleanup for your operators at the end of their production run or shift.
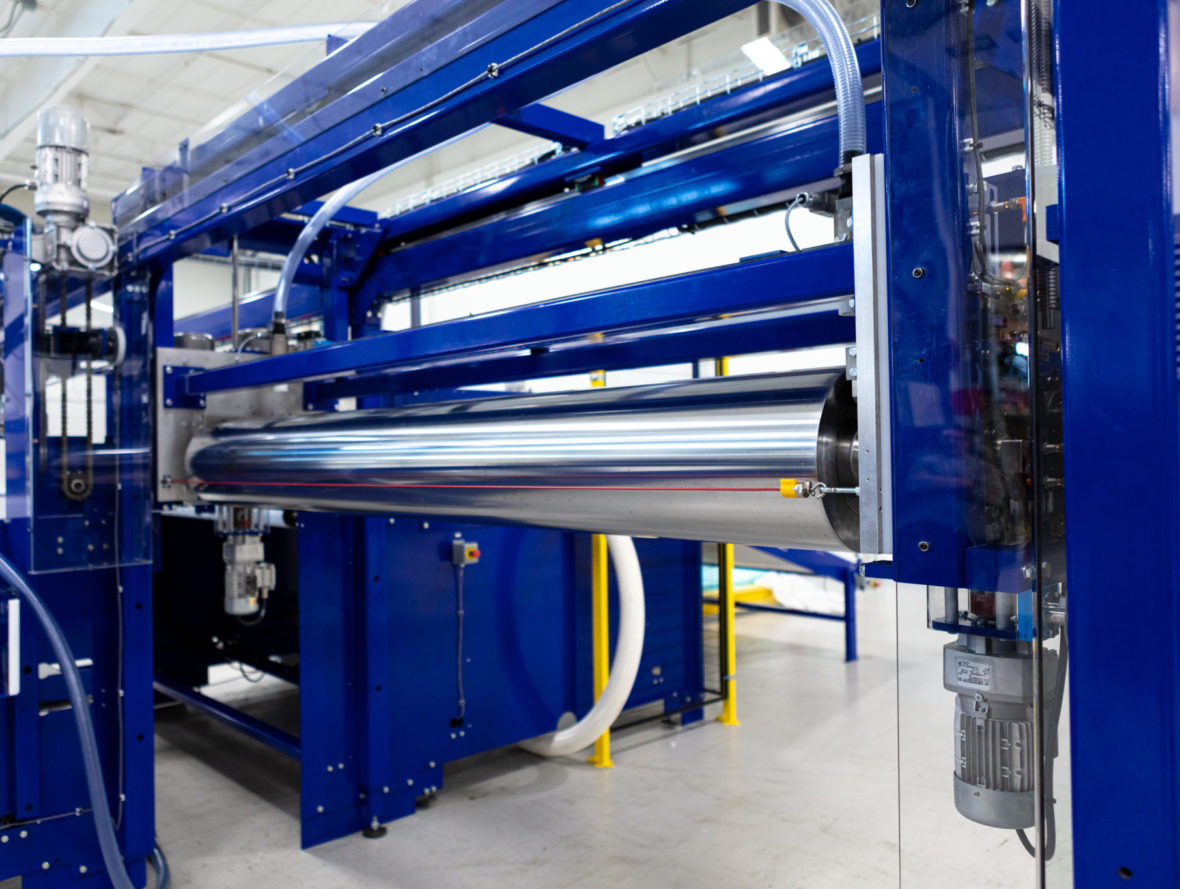
Producing superior mattresses does not have to come at the expense of high adhesive usage or slow production rates. C3 roll coaters, especially when combined with synthetic latex adhesives, will help you fulfill your quality standards and production goals. Contact us today, and our team will help you find the right lamination solution for your operations.