Machine operators play a critical role in producing quality mattresses, and that starts with your lamination crew. They set the pace for the rest of your line, and they have a fast, keen eye for checking edge alignment. However, most existing methods for building a laminate require operators to handle multiple manual tasks per bed, making the process labor-intensive and time-consuming. If your facility experiences high turnover in these positions, it’s holding you back from maintaining a well-trained, quality-focused workforce.
When we designed the LCN1250 Lamination System, improving operator ergonomics was top of mind. We sought out an automation solution that worked seamlessly with the lamination team. The result is a semi-automated machine that handles each layer’s initial placement and reduces the manual labor, leaving small adjustments to the operators. It also keeps them distanced from one another and limits their contact with both the machine and the product. In this edition of STANDOUTS, we’ll focus on how the operators’ job is simpler and safer on the LCN1250, while still maintaining high throughput. Watch below!
The LCN1250 runs standard with four operators – two placing layers at the infeed and two at the build station. Here, we’ll walk through the line and highlight how the LCN1250 improves the operators’ tasks at each station.
Improved Ergonomics At The Infeed Enhances Production
The ease of use throughout this machine begins with how operators work at the infeed. First, the infeed conveyor angles downward towards the operators for ease of placement. Here, operators keep their movements below the shoulder and above the knee, where body mechanics are most efficient. Pallet lifts installed at the infeed also help keep raw materials off the floor and limit bending. Operators may choose to advance layers with a push button or a photo-eye to trigger conveyor movements. Work at this station is the most labor-intensive part of the LCN1250 lamination process.
Next, infeed operators run the layers sideways, or so the leading edge is the length of the mattress. We use this method on all of our lamination systems to reduce reaching and straining. The length is the most consistent among all sizes and varies, at most, between 5-9 inches. For example, a King and a Twin mattress differ in length by only five inches, but the width differs by 38 inches. Imagine you run beds along their width but the conveyor’s width accommodates King sized layers. Your operators would lean almost eight times farther over the conveyor to stack and adjust the layers on a Twin. By running the layers sideways, operators keep all their movements closer to their body.
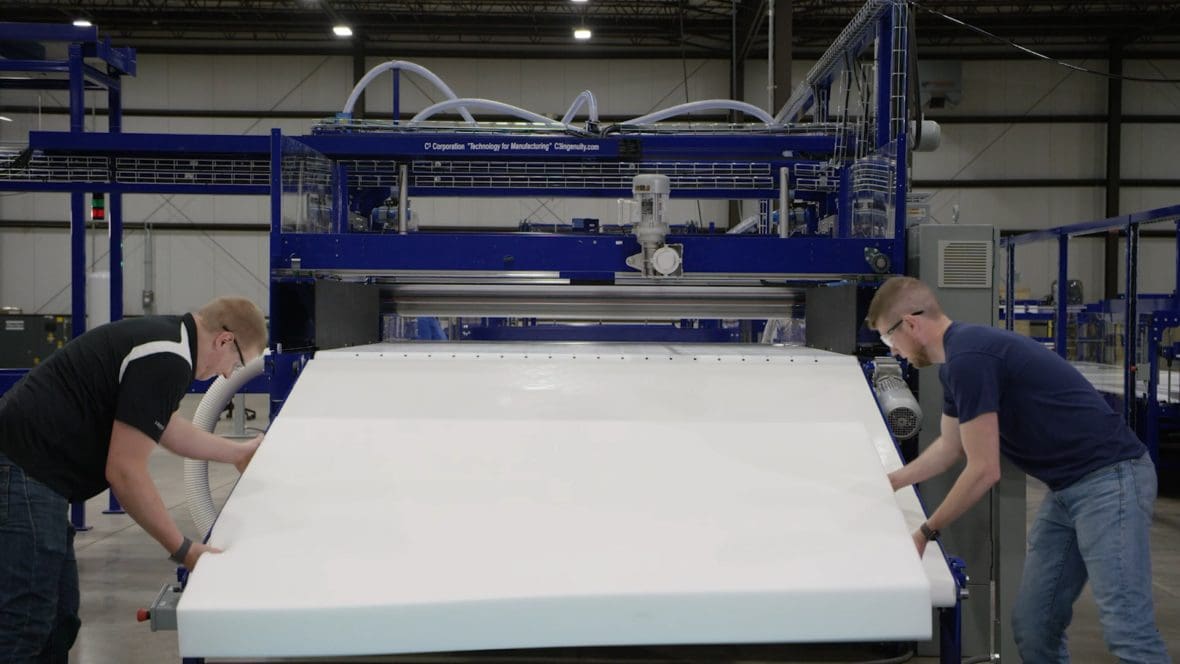
Lastly, the operators contribute to the accurate placement further down the line by aligning an edge of the foam to either a guide rail or a line on the conveyor. When the infeed operators use this guide, it leaves the two build station operators responsible for monitoring front and back edge alignment. Next, we’ll see how the build station’s transformation reduces the remaining adjustments and labor.
Build Station Safety Improved By Auto-stacking Technology
Once the layers receive a coat of adhesive, they convey to the build station. This is where you’ll see the most significant change in labor with the LCN1250. In the past, you would expect to see operators stack layers by hand. They would lift each layer, walk sideways while carrying it, and place it atop the rest of the build. This method involves a lot of unsafe twisting and increases the risk of tripping, all while carrying a heavy, adhesive-covered piece of foam. As the build gets taller, the operators need to lift higher; the higher they need to lift, the greater risk for shoulder injuries.
Instead, the LCN1250 auto-stacks the layers and eliminates all these extra unsafe steps. Operators no longer handle any layers until the machine has already placed them. Instead, they focus their efforts where they are most efficient: adjusting edge alignment and monitoring quality.
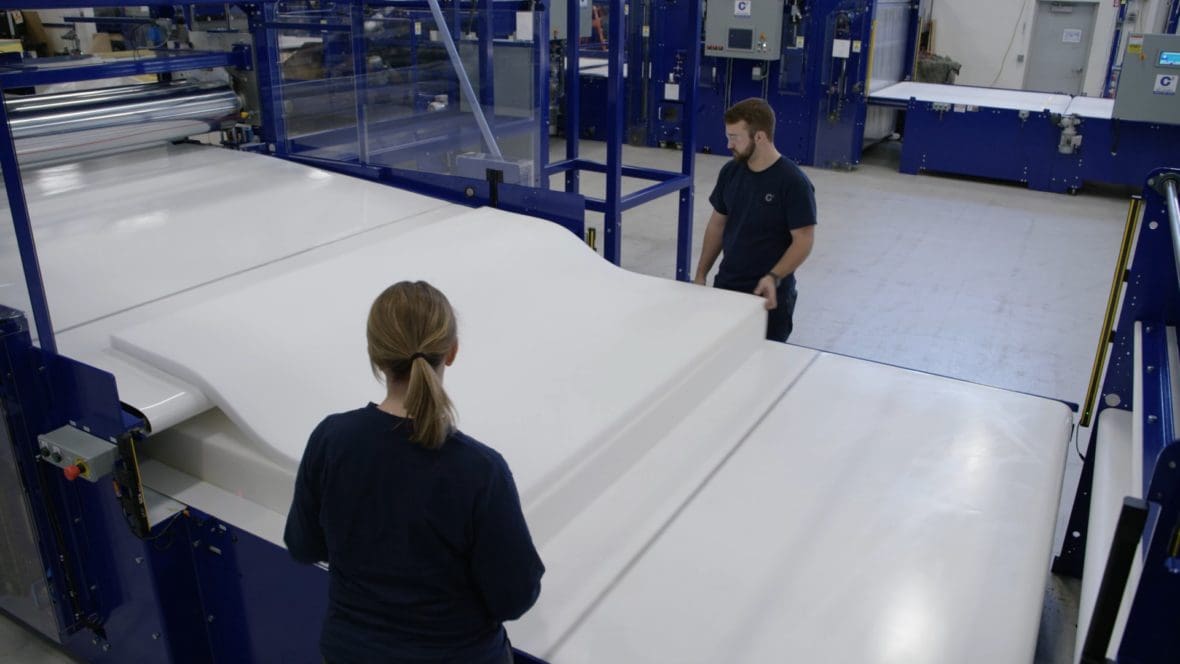
Simplified Adjustments Boost Focus On Quality
With the machine handling the initial placement, build station operators are left to align the edges. The infeed operators have already set the short edges using a guide, leaving the front and back edge alignment to the build station operators.
The LCN1250’s recipe controls allow operators to refine layer placement, limiting manual adjustments as much as possible. In STANDOUTS: Lamination Placement, we saw how the LCN1250 auto-stacks the layers with +/-1 inch accuracy. This limits operator movements to a few simple flicks of the wrist and leaves them to focus on making small but essential alignment adjustments.
Running layers sideways also helps build station operators keep their arm movements closer to their body. If operators must lean to tug a piece of foam into place, they’ll spend less time in an awkward position because the machine has already handled the initial placement.
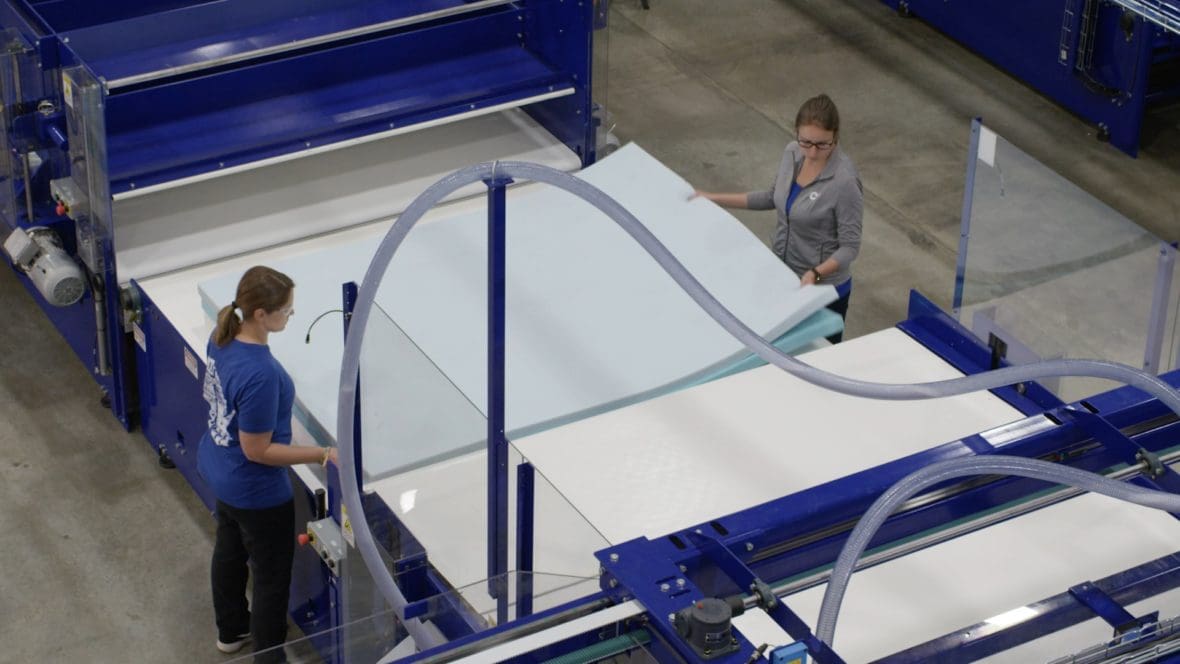
The build table height is also set so that operators make all adjustments above mid-thigh and below the shoulders. Combined with the limited reaching, this lets operators work within the safest range of motion, known in occupational safety as the power zone.
The result of this redesigned build station is that operators adjust layers much faster, with lower effort. They’ll find themselves less fatigued while actively engaged with production quality more than ever before.
Built-in Social Distancing And Limited Contact Mitigates Exposure
If you’re following social distancing guidelines at your facility, the LCN1250 features will give you peace of mind. The conveyors are all over seven feet wide to accommodate the longest mattress size; whether working at the infeed or the build table, this machine always keeps operators spaced over six feet apart.
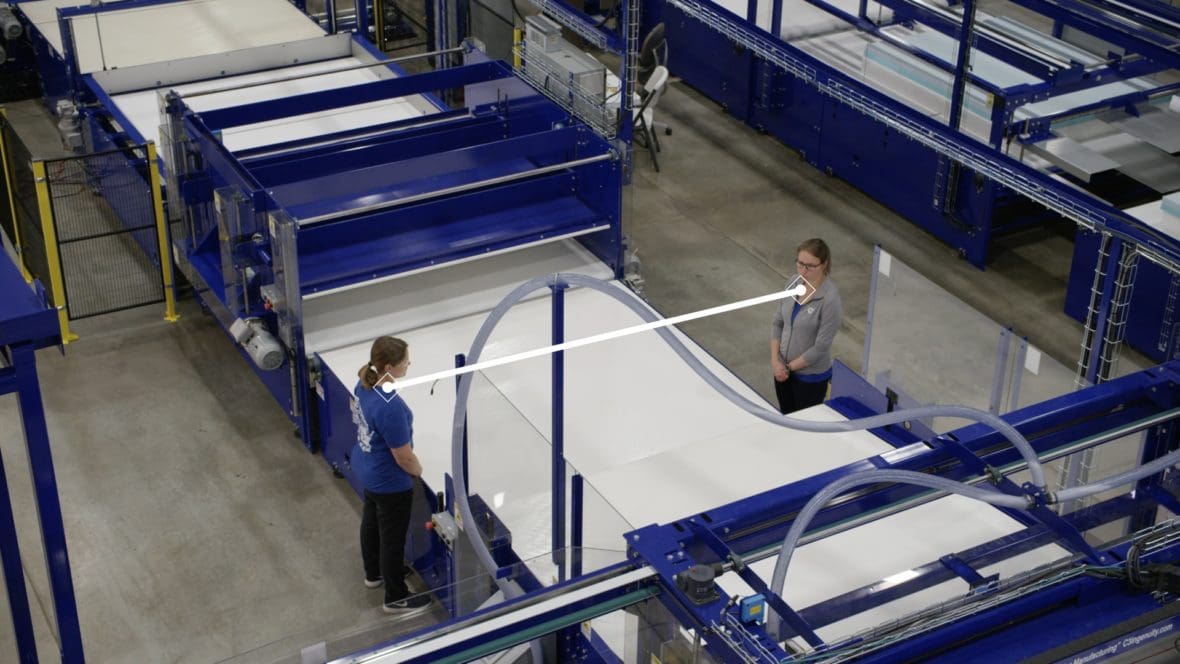
The design also reduces touchpoints by limiting the necessary contact operators have with both the machine and the products. At either station, operators have the option to set the machine to run with a more automatic flow by using photo eyes, rather than requiring push buttons to advance every layer. Build station operators also make minimal contact while adjusting the layers when compared to the sustained contact required while lifting and carrying them. This reduces the number of surfaces that could be contaminated and affect staff at other stations down the line.
The LCN1250 design lets operators shift their energy from throughput to quality, meaning they focus on producing a higher caliber product. Alleviating that pressure to keep up makes your operators’ work more rewarding. Now, the machine handles the most laborious and time-consuming tasks, and operators at all stations contribute to final edge alignment. By first evaluating existing lamination processes, we developed the LCN1250 to provide a solution that eases their physical workload while keeping your crews distanced, safe, and productive. Are you looking to review labor resources in your facility for areas of improvement? Contact us today to discuss your options with our team.