Creating small, easy-to-ship packages is in increasingly high demand, but compression packaging machines are not-one-size-fits-all. If you’re looking for an affordable way to enter the roll-packaging market and you manufacture a variety of products that don’t require folding, the RC9500 Roll Cage System may be the right machine to help you accomplish that.
Watch the video below to see examples of products the RC9500 packages.
The RC9500 is a cost-effective way for foam and bedding manufacturers to start leveraging the benefits of roll packing. It processes products up to 90 inches wide and 16 inches high, and rolls them to final package diameters between 9.5-13.5 inches. Some products the RC9500 can roll-pack include:
- Standard mattresses – from Twins to Cal Kings, made of all-foam or with pocket coil/innerspring bases
- Smaller beds for RVs, bunk beds, cribs, etc.
- Toppers made of foam and latex – ran flat or manually folded in half or thirds for smaller package sizes
- Individual foam cores or layers
- Pet beds, wedges, foam mats, etc.
The minimal design of the RC9500 requires less space and less packaging material than more robust compression machines. The base model consists of an infeed conveyor, a stretch film cart, and a roll cage. This makes it the smallest footprint of any of our compression packaging machines capable of packaging 90 inch wide products. It also operates at a low cost per package thanks to its use of only stretch film.
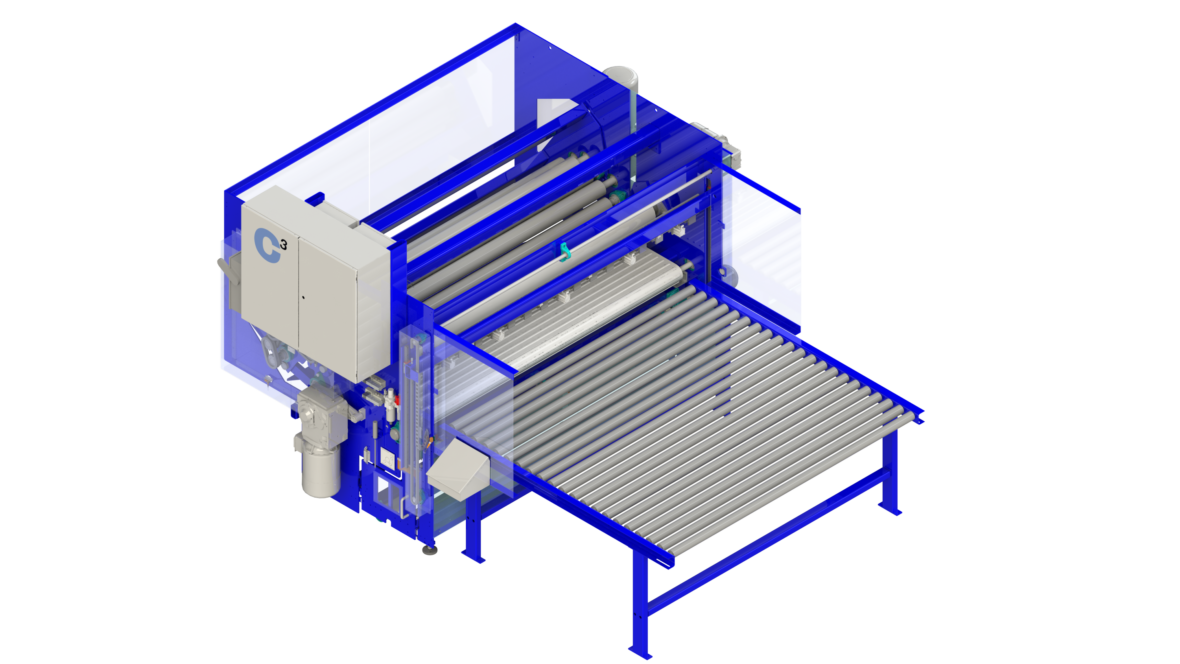
By combining compression and rolling into one step, the RC9500 packages products at a rate of up to 120 units/hour. It’s also flexible enough to jump between different products without the need to stop for reprogramming. If you are looking to monitor your film usage, though, the HMI does allow you to customize some of the roll cage recipe controls.
The RC9500 accommodates both 50- and 100-inch stretch film, so you can swap to the appropriate film size when switching between product widths. Alternatively, you can upgrade your machine to include a traversing stretch cart, which uses only 50-inch film but will travel the length of the product to fully wrap each one. This is a great time saver if your facility handles short runs or has frequent product change-overs. At most, operators will need to make simple recipe changes on the HMI between runs versus awkwardly swapping out film sizes every few hours.
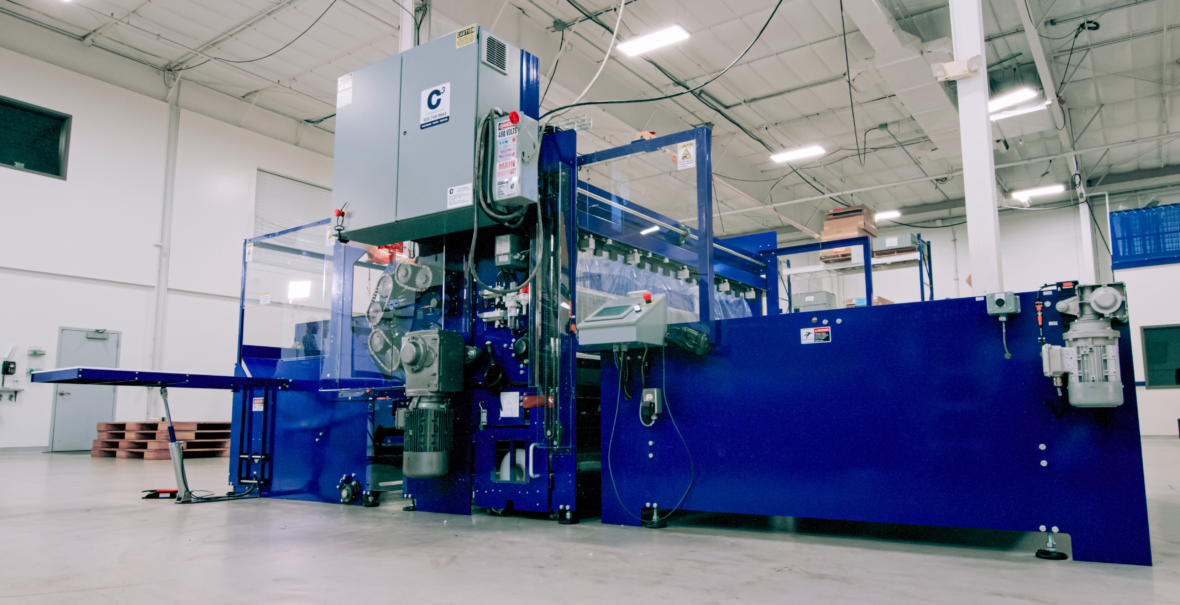
Besides traversing stretch, there are two other main ways you can upgrade this machine to better suit your production needs:
- Boxline – As seen in the video, the boxline add-on conveys wrapped products up to waist height, where the operator then uses a foot pedal to transfer the product to a box. This equipment provides an ergonomic alternative to lifting products from floor level and manually placing them in boxes.
- Variable Cage – If you’re still looking for more packaging variability without the need for folding, you can also opt for a variable roll cage on this machine. This would increase your final package diameter range from 9.5-13.5 inches to 7.75-19.5 inches.
Reaping the benefits of compression packaging for storage, shipping, and e-commerce doesn’t have to start with robust, expensive equipment. If you are looking to roll pack a wide variety of foam products in one machine, reach out. Our team will help you evaluate your product mix to see if the RC9500 is the right entry-level packaging machine for your facility.