Placing layers of foam atop each other to build a laminate has typically been a labor-intensive process. When we released the LCN1250 Lamination System, the new functionality of a merge table helped operators complete the placement task by taking care of the lifting and placement of each layer.
The new system is intentionally semi-manual to make the best of both automation throughput and the operator’s finishing touches. This unity allows facilities to take advantage of optimal throughput and produce more quality finished goods.
When each layer of a mattress aligns well, the bed has nice, even edges around the mattress perimeter. See how the LCN1250 handles layer placement to achieve this goal in this video:
Determine What Tasks The Machine And Operators Do Best
One of the ways in which the system helps improve product quality is by allowing the operators to focus on what matters most – well-aligned layers. Yet, that’s not all an operator is responsible for on a traditional lamination machine.
Operators stationed at a traditional lamination build table have a number of tasks to complete:
- Retrieve the laminated layer.
- Lift and shuffle it to the build table.
- Lay the layer on the mattress build.
- Adjust edges for accuracy.
Efficient use of operators’ movements means each step should add value to the end product’s quality. If it’s not, it may not be an efficient use of energy. These are often steps that can be automated and handled by the machine. So, what steps add value?
Step 2 of lifting and shuttling the layers of a mattress is awkward. Anyone who has tried to do this for the first time is likely to have gotten glue on themselves or lost control of the product. Some layers with high densities can also be quite heavy, making it even harder to lift and move an already flexible material. The movement in Step 2 is strenuous on operators, especially when repeated over time.
Step 4 would be most critical for building quality product. This is when an operator fine-tunes each layer’s alignment before sending it on through the production line. We heard from clients the fine adjustments by operators at this step are essential to product quality, and therefore, should be the focus of the operator’s role.
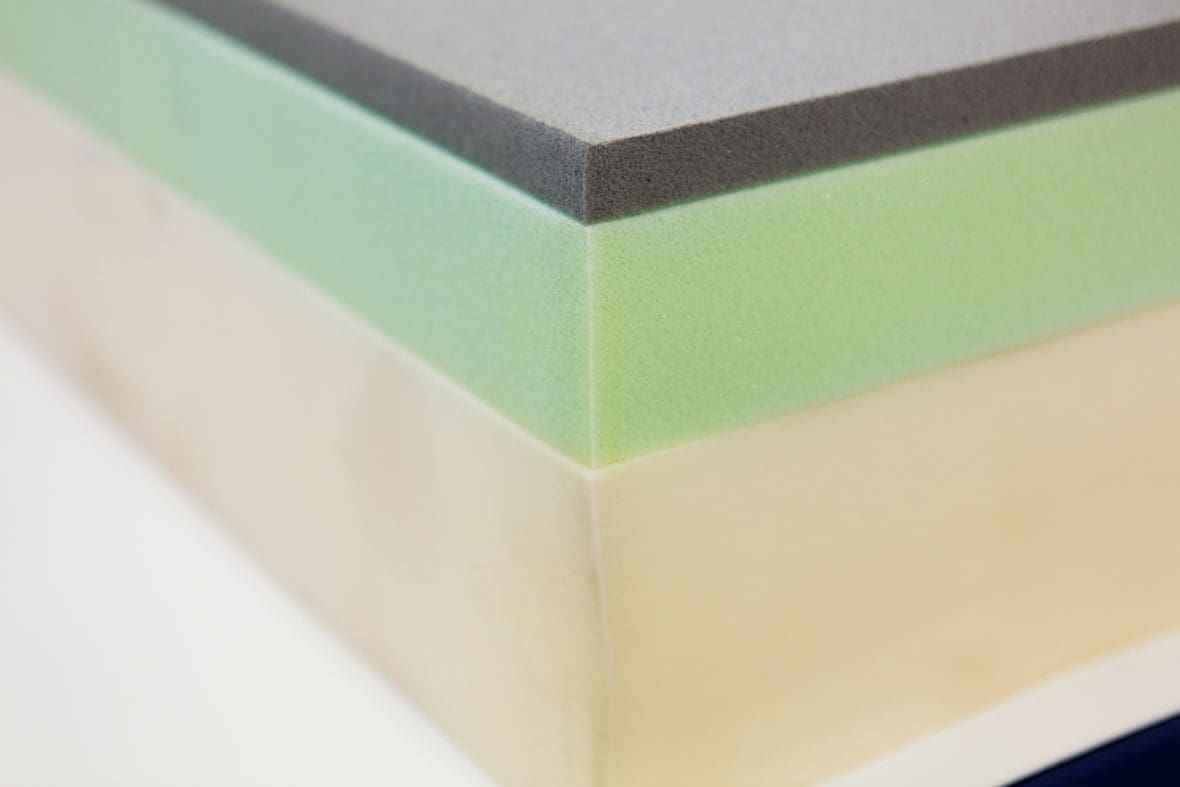
How The LCN1250 Places Foam Layers
The lamination machine’s merge table shuttles the layer to the build station and pivots it to lay it atop the other layers. Placement is done within one-inch accuracy. This is possible due to the alignment at the start of the infeed of the machine. Then, the silicone belting on the machine is able to hold that edge in place through the roll coaters and to the build table without slipping or moving.
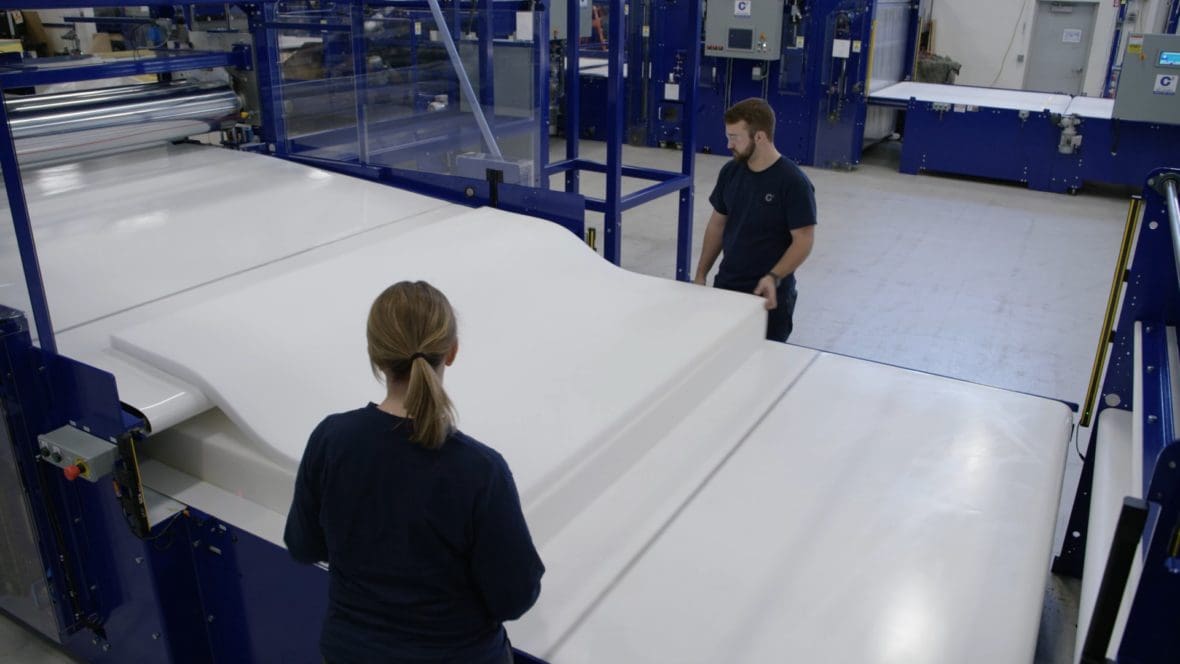
These features allow the operator to focus on small adjustments to the laminate before it’s finished and sent off to the tamp press. Product is now more likely to be built accurately and with good edge alignment because of how this machine aids in the build process. The operators’ job is also simpler and less labor-intensive with the machine handling the lifting and initial placement. This is an ergonomic bonus and makes working at this station less of a physical strain.
The LCN1250 does more than laminate layers, it helps operators with the most essential task of building the bed itself. Learn more about the LCN1250 and other lamination systems here or in this quarter’s issue of Eng*nuity magazine.