As C3 grows, so does our vision for the future. In 2017 we added on to our headquarters, and in 2018 we expanded to a second location across town. With each new growth spurt came new opportunities, and we soon found ourselves overfilling these spaces, too. In late 2019, we sought a building where we could increase our warehousing potential while also reserving a dedicated space for testing new concepts. We found such a building less than a mile from our headquarters, and in early Q2, we officially moved in.
Our new Marshall building consists of over 100,000 square feet, with 87,000 square feet for manufacturing and warehousing. This move plays an essential role in our operations and supply chain while also opening new doors for our research and development team. Hear from John, our VP of Operations, and Joe, our CEO, on the value this new location brings!
Streamlined Supply Chain And Expanded Inventory
The Marshall building will serve many of the same purposes as our Lyndale location did, but with higher capacity. “As a company that’s growing very rapidly,” says John, “we need the space to grow. We need the space to receive the equipment and parts we use for the assembly and production of machinery.”
One fundamental objective of increasing the space for parts storage and sub-assembly is reducing lead times, and the space at Marshall lets our assemblers keep the build process moving. Our Shipping/Receiving team receives the initial parts orders here and kits them for the assembly team. Then, assemblers at Marshall have ample room for building sections of each machine. They later move these sections to Venture for final assembly, wiring, testing, and run-off. This process keeps projects in constant progress – as finished machines move out, new machine sections move in.
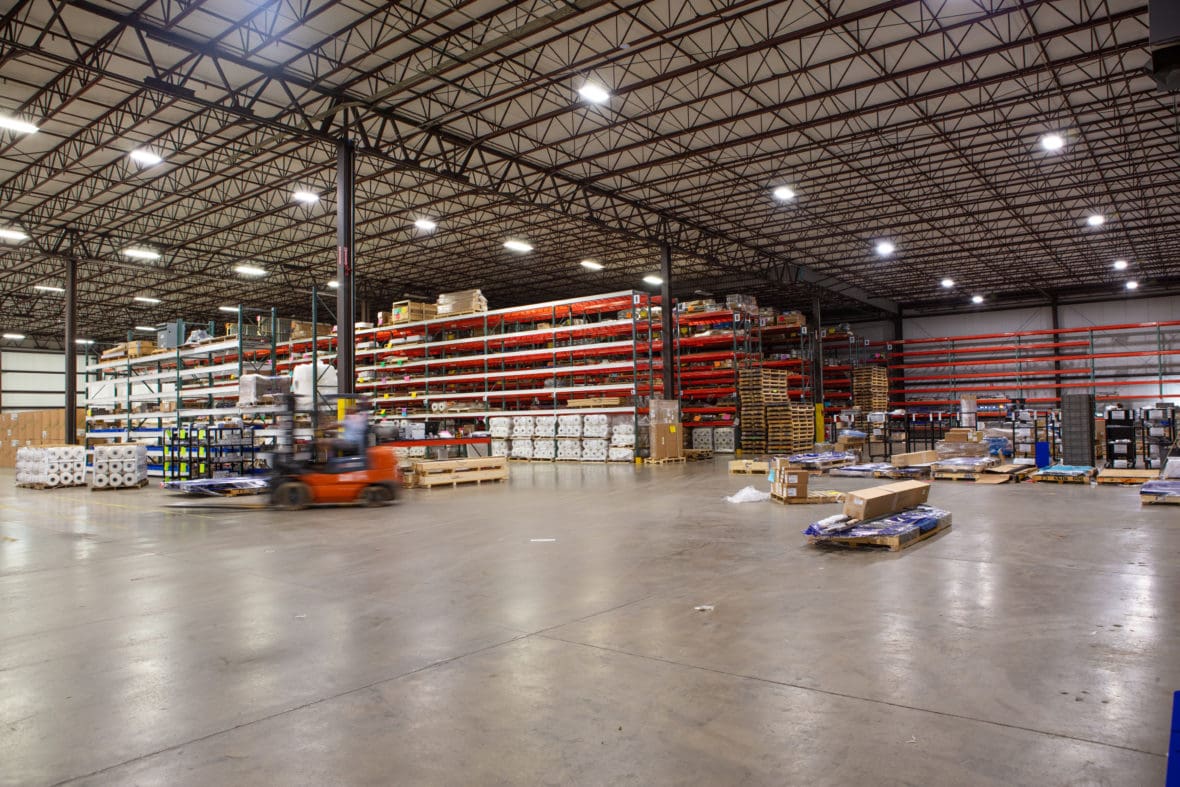
This additional space means we’ve also increased our on-hand spares and consumables inventory. Maintaining a steady supply of these items means we ship them to our customers faster, and we have more potential to expand the consumables we offer. “Everything we’re doing in operations and supply chain is about serving our customers and better delivering to them,” John says.
Dedicated Space For Research And Development
Even after transferring most of our warehousing to the Marshall location, we still had plenty of room to capitalize on a unique R&D opportunity. Here, we’ve installed a full production line starting with an LCN1250 Lamination System and ending with a CF1396 Compression Machine. The line also includes trim saws, a destacker, pushers for covering stations, and a Force Deflection QA system. By tying all these pieces together, our engineers can test and gather incredible insight into how these pieces of equipment work together and impact the final product.
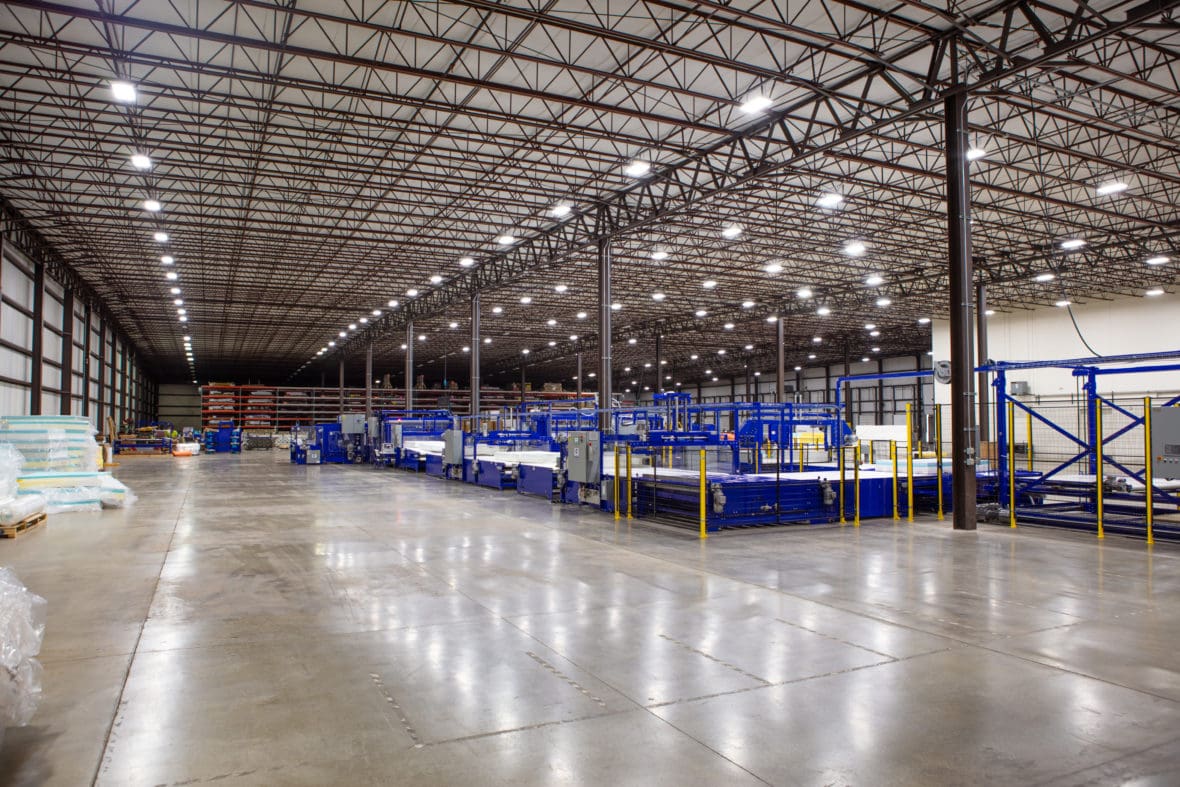
They’re also testing how their new concepts integrate with our existing designs. “This gives us the opportunity to do something new: to put a full line of machinery into production and innovate and be creative in the manufacturing process,” John says. “In doing so, we have a line that allows us to learn and demonstrate what operational excellence looks like.“
This line serves as a showcase piece for reaching our clients from a distance, too. With uncertainty around travel, our team began implementing tools for virtual demos on the Marshall line. It’s a way everyone stays safe and healthy while staying in communication with our clients. We’re excited about the discussions and learning that this dedicated line will bring.
The insights and innovations that come from the work taking place at our new Marshall location will be invaluable to our customers and us, and we look forward to sharing them with you. Contact us today to schedule a virtual demo with one of our account managers and see this line in action for yourself.