The development of our variable roll cage technology involved more than simply allowing for roll cage adjustments for wider or narrower package diameters. That’s nothing new; there are many packaging machines that can make these types of adjustments. Because of this, when we set out to add this feature to our packaging machine, we not only wanted to make it adjustable but also teach the machine how to adjust automatically based on every product that passed through its infeed.
When we work with clients to discover the right packaging options for their products, we always start with using our roll cage calculator. This calculator uses product specifications to determine safe end-package dimensions. In order to accomplish our goal of automating the adjustable features, we figured we could import the functionality of our calculator directly into the HMI programming of our machine.
What we developed became known as our “smart packaging features.” These features take the analog functions of our roll cage calculator and automates them into the coding of our packaging machine. This allows every product to be measured and the machine to adjust the roll cage to best protect the package’s integrity. We sat down with our CEO, Joe, and our lead mechanical engineer for compression, Jeff, to talk about what went into these design decisions and what they mean for you and your operators.
The productivity of the variable roll cage, Jeff tells us, starts with the roll cage calculator. We’ve talked about the roll cage calculator in regards to packaging blocks of foam in Issue 3 of Eng*nuity, but if you’re not familiar, it looks like this:
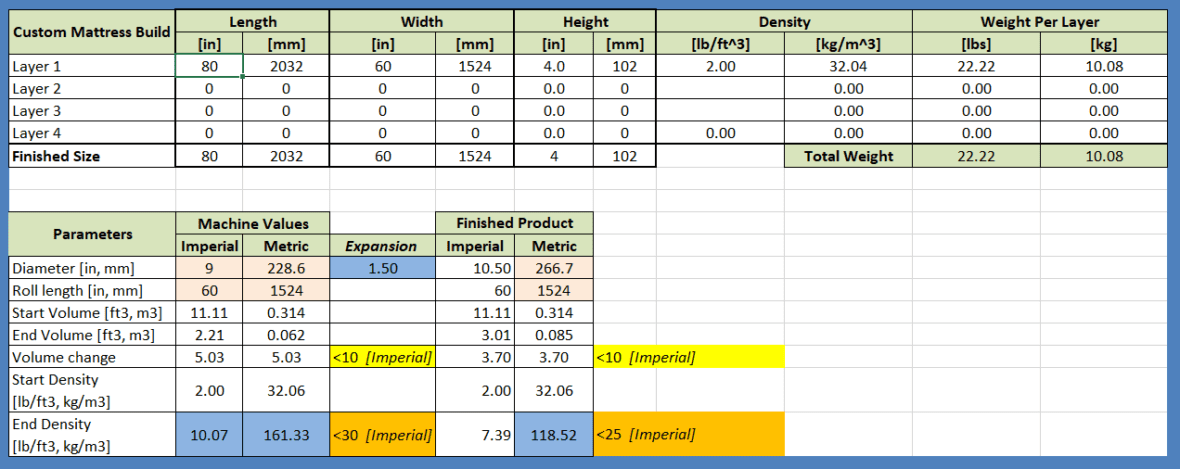
As you can see, this tool takes the starting dimensions, weight, and density, then calculates the anticipated volume and density changes when compressing and then roll packing. This tool is often used in a planning phase to select machinery or determine ideal packaging for a product. Once in production, however, there’s the risk of error with incorrect inputs or production errors from further up the line. If this happens, you start to risk damaging your product, potentially shipping poor quality product to customers, or damaging your machine.
Our compression engineers determined that the machine could be fitted with a few extra measuring devices and calculate this itself in real-time. The press of the machine was already equipped to monitor density and volume changes, so adding a scale to weigh the incoming product and sensors to measure its dimensions would allow the machine to carry out the calculations. The calculation would then trigger the roll cage to adjust accordingly based on your facility’s tolerances.
Along with making the machine “smarter,” putting this technology into the machine itself also empowers your operators. When there’s a lot of production variation coming through your facility, these features help your team stay consistent without unnecessary reliance on operators to remember important product information.
As Joe explains, “We thought it was important to get that tool off of our laptops and onto the machine, closer to the operators and closer to the business. If we integrate the tools, the operators will use them every day. And if they use them every day, they get a better understanding of what they’re doing and why it’s important. When they see these calculations day in and day out, they’re going to get a better understanding of how to control what they’re packaging. It makes everybody smarter by integrating these tools on the machine on the floor.”
Want to learn more about how to use these features or the roll cage calculator? Check out this month’s issue of Eng*nuity’s SKILL feature.