The mattress manufacturing industry has only seen the tip of the iceberg in terms of the changes that we’ll need to make in a post-pandemic world. New recommendations are coming from national and state governments that have immediately impacted business operations, and now we’re seeing those restrictions lifting with cautions in place. It seems one thing is for certain: the way we do business will have permanent changes. How will businesses adapt successfully with minimal impact on operations?
While many businesses are still under reduced operating restrictions or have pivoted to help by sewing masks or making hospital beds, it’ll soon be time to think about how to reopen to full capacity. To do this, you’ll need to reconsider how your operation can adjust to keep your employees safe and healthy.
When we looked at workforce management, operations layout, and the importance of remote capabilities, we created the following insights for how mattress companies can respond to the changing manufacturing atmosphere.
Be Smart About Automation Adoption
Inherently, automation supports social distancing and minimal human interaction for handling products. By no means does this mean the solution to a post-pandemic world is to automate everything and rid of all employees. There are, however, key areas we can consider automating to reduce the number of people necessary to produce.
When reviewing your operations, ask yourself a few questions: What processes pose the most risk for operators? What tasks are best handled by a machine instead? Where can we redistribute work so fewer people are involved with production?
Lamination is one area to consider, especially if your team is still using spray-application. Our newest LCN1250 is the most automated version that handles and glues the foam with minimal operator involvement. Some manufacturers can opt for the original LCN1000 machine, which supports a one-man mode where one operator can run the machine and make beds. The choice will depend on your mattress production volume, but both systems use different levels of automation to reduce the number of operators needed and their handling of products.
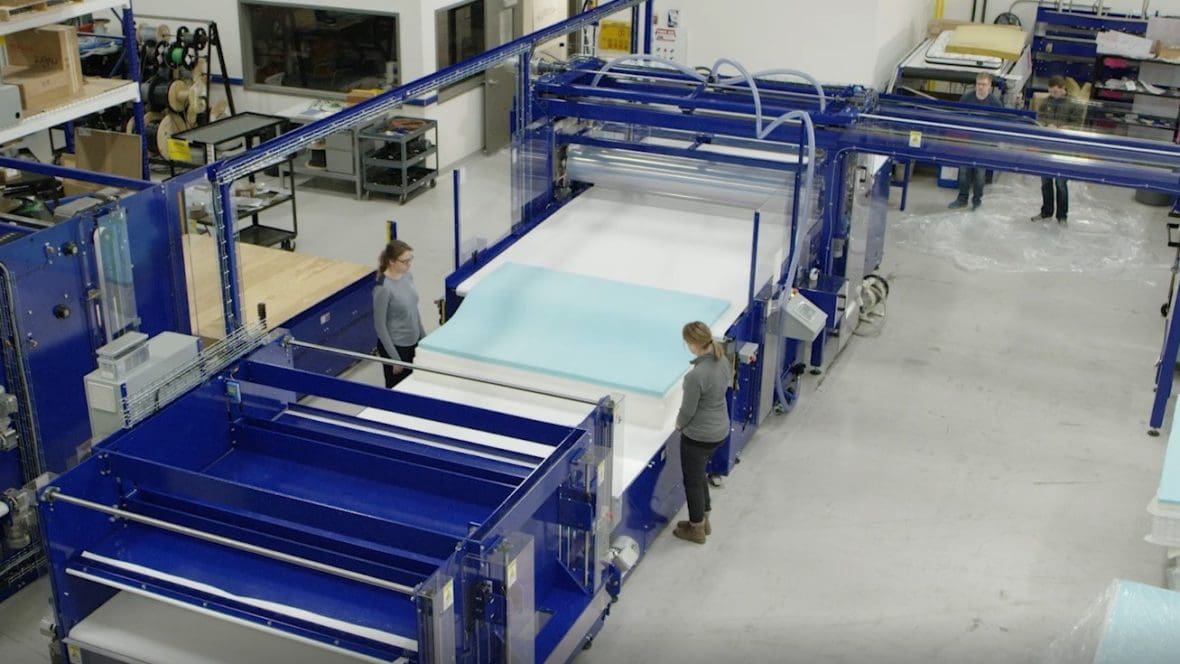
For manufacturers that have lamination equipment like this already in place, they may be facing issues with having enough product to run through the machine to keep the line running. Accumulating products at critical points of manufacturing – like before/after laminating – can help make sure operators have work to do at their stations when they’re in the facility. Accumulation can also reduce handling by individual operators. For example, a stacking unit after lamination would automate the stacking of laminates and convey them to the next station without operators needing to lift and move them.
Depending on how you’re operating today, adding machinery to certain production areas can help further automate workflow, increase spacing among employees, and decrease the number of employees necessary to run production. One way to get the full picture of this is to consider your production line layout.
Modify Production Floor Layouts to Support Distancing
Production layouts may need adjustments as we look to provide safe distances among employees for their wellbeing. Issues arise when there are employees congregating in one space or if multiple people are needed to support a single line of production. For example, a line will have its crew of operators, but there may also be another employee who stops at the machine for PM checks, another who services those issues, a line supervisor managing the crew, plus a plant manager walking the floor multiple times a day. You can quickly see how even a line that may need fewer operators to run is still supported by many others, which brings added risk to the team.
Cross-training is a great way to reduce the number of people needed to support the line, but you may also consider how that line is laid out. A pod-style line is one of the most popular layouts right now, as it allows employees to stay central to their equipment and limits the entry/exit points of additional supporting staff. For example, the line layout below may be more pertinent in times of social distancing:
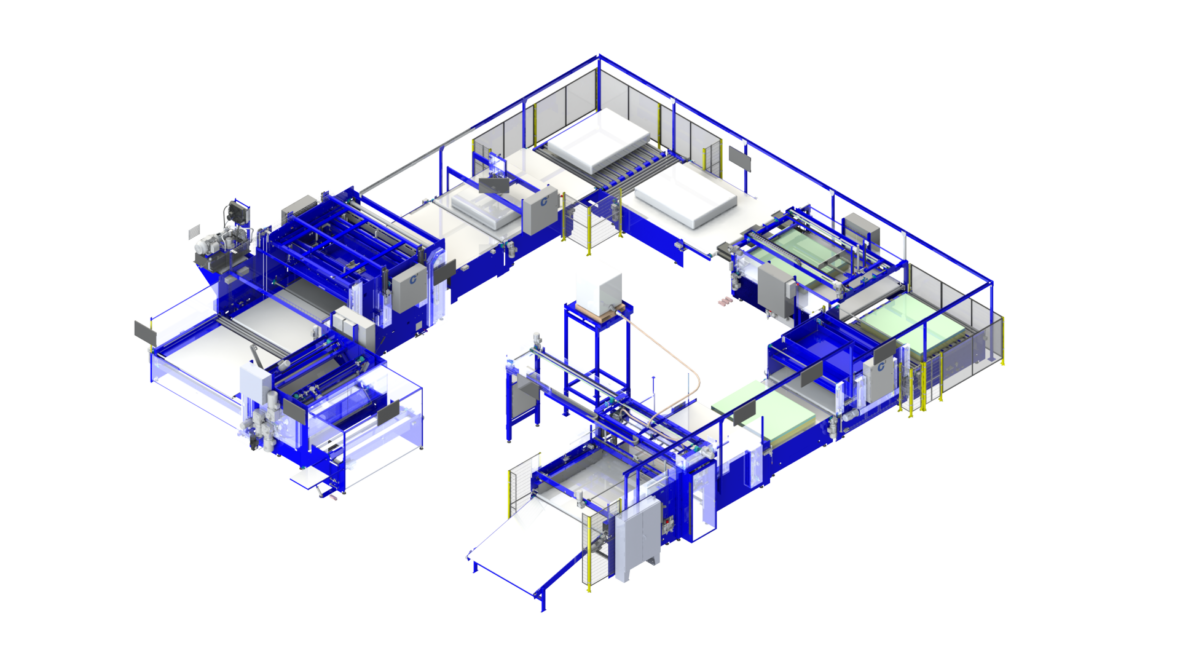
What happens here is employees can work within a smaller square footage than if the line was linear and they had to traverse the entirety of the line. The entry and exit points are also in the same area, which can make for a protected single drop off and pick up point for raw material and finished goods. For different activities, these lines can be duplicated on the floor to support separated work teams and keep them dedicated to a single area of the facility while still being productive.
Rely on Vendors for Remote Maintenance Support
Regardless if you’re looking at capital purchases, you will be more attuned to maintaining the equipment you already own. It’s even more vital now with travel restrictions in place that prevent service techs from visiting facilities. It’s also likely your own facility will have more restrictions on outside visitors. Because of this, it will be crucial to follow proper preventative maintenance practices and perform routine checks on machinery to catch any issues early.
C3 has always supported our machines remotely with VPN capabilities. VPN allows our engineering team to access your machinery and see the status of the machine’s Programmable Logic Controller (PLC), drives, and other devices connected to the machine via ethernet. Having access to the PLC allows our engineers to see the states of devices, check if they are operating correctly, and diagnose the problems the customer is experiencing. We can also confirm recipes are created and setpoints are changed correctly, as well as any other mode changes you need. The VPN also allows us to make program updates if a customer needs something new to be added. C3 has also responded to the travel bans by increasing our services offered remotely. Teams have been on call to respond quickly to service issues and help with machine startups.
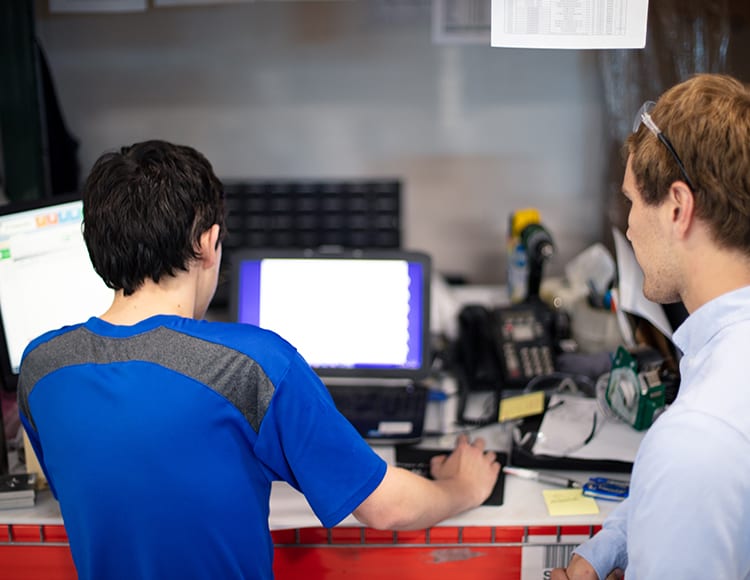
Use Data To Predict Maintenance Issues Sooner
Many supervisors right now aren’t able to walk the floor or may be working remotely, so it’s more important than ever to receive meaningful feedback on machine performance and upkeep. Regular checklists or maintenance logs may not be enough to give supervisors the information they need to ensure the machine is operating appropriately. To mitigate risks, supervisors should create daily logs of preventative maintenance work and cleaning activities. These daily checks will give supervisors additional data from the floor to recognize any potential issues.
Detailed logs also help if you do have an issue on a machine. It’s much easier for vendors like C3 to diagnose an issue if we know the machine’s condition and the levels of production it’s been involved with.
It’s also a good time to take inventory of the spare parts kept on hand at your facility. If there are critical spares not in your possession, see about getting them on order so you’re not waiting for extended lead times due to the effects up the supply chain.
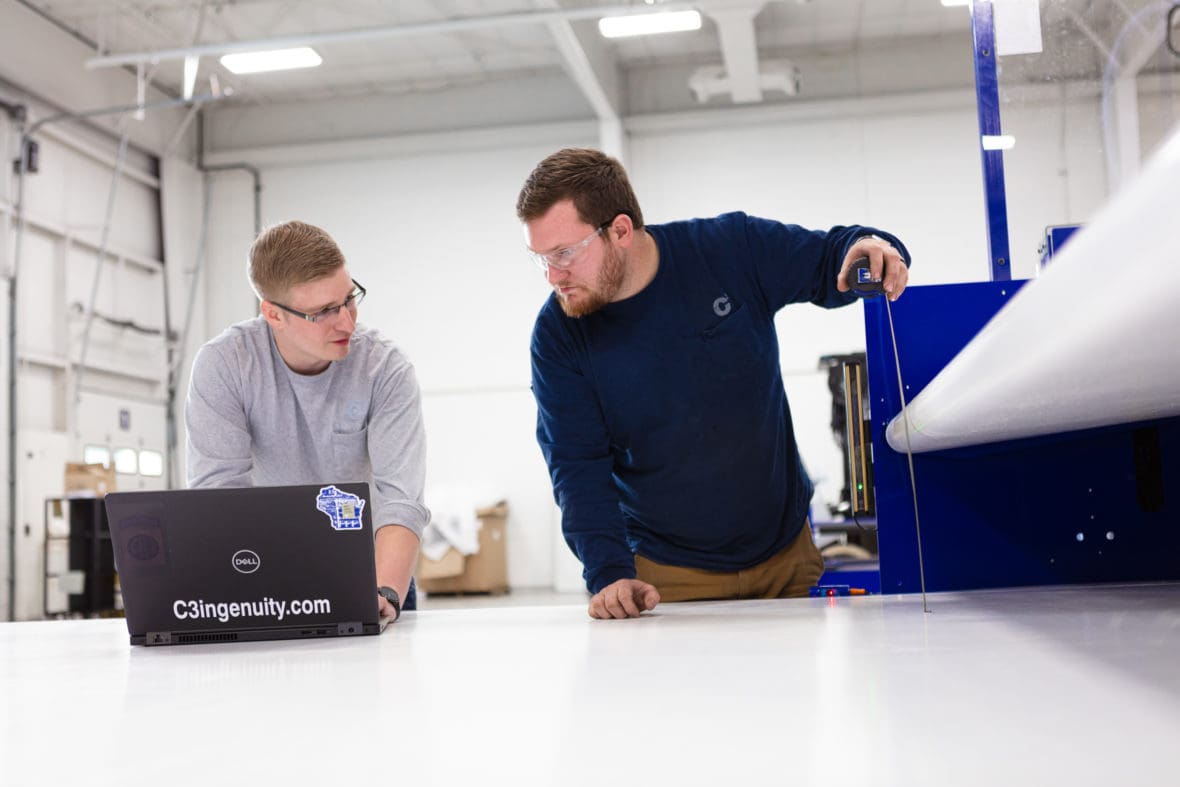
What C3 Is Doing
This is an odd time for manufacturing for us all, and as fellow manufacturers, we’ve also had to redesign how we do business. Much of our focus in these few weeks has been on turning to virtual tools to assist customers with startups, installs, and general services. We’ve also been able to continue machinery production, as well as keep our parts and film products available for customers who need them.
Like many companies, we’ve also taken time to cross-train employees. Especially in our service department, we’ve focused on roles that can widen their skillset so they can be more helpful independently. We are skilling up so that when we can send out our technicians to help customers, they will be more prepared than ever to address your machinery concerns.
If you need help evaluating your production for automation opportunities, restructuring your production line, or with services, parts, or film supplies, reach out to our team. We’re here to help with a successful transition to this new normal.
Would you like to get news and updates like this sent directly to your inbox? Click below to subscribe to our newsletter.