With the innovation of our variable roll cage and the second roll cage (MC1434) for the compression folding system, it is now possible to better protect products and rely less on operator involvement to package a bed. Plus, the combination of technologies allows some products to reach even smaller package dimensions.
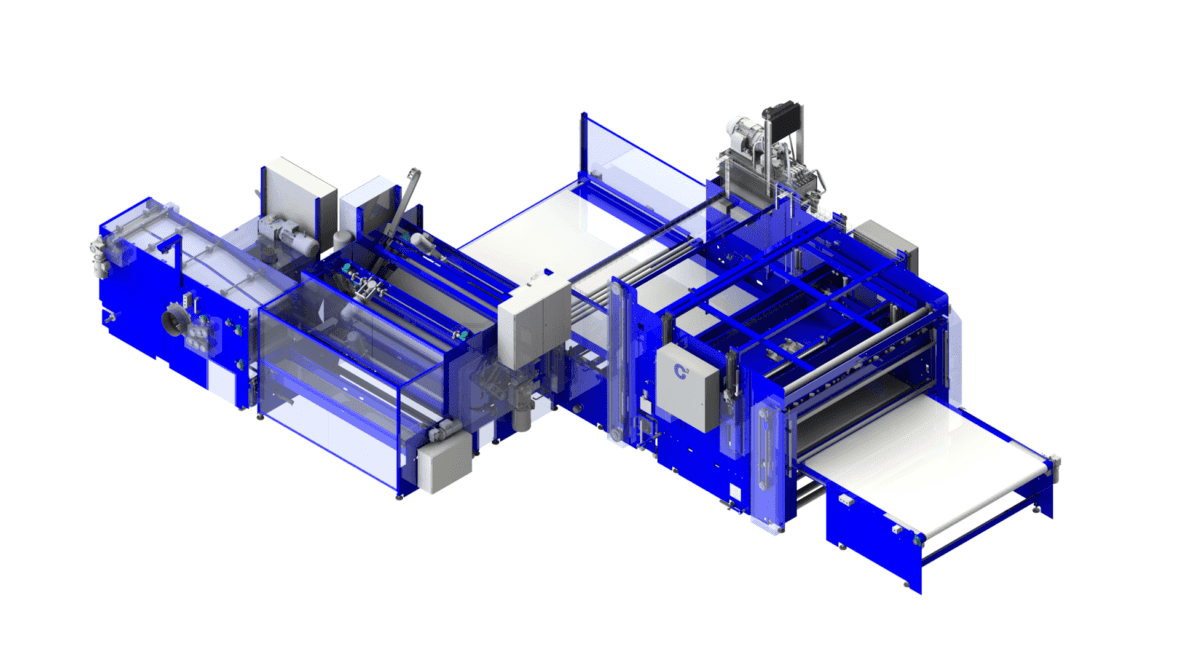
These innovations provide multiple benefits when used together. For example:
- “Smart” features protect the product so it isn’t over-compressed or damaging to the machine.
- Machine auto-adjusts recipes based on measurements, resulting in less reliance on operators for these tasks
- A wider range of product sizes can be packaged in the same machine.
- Reduced cost per package for double-rolled beds.
Let’s look at two of these factors in detail: the improvement of the operator’s work and the new measuring devices of the machine.
What Makes The Machine Smart?
The “smart package” is what we’ve been calling the product that exits our compression folding system when it’s equipped with a variable roll cage and updated HMI software. You’ve heard before how we use a compression roll cage calculator to determine the potential package dimensions for a product. Now, our engineering team built that tool directly into the HMI software so it’s completely integrated in the packaging process of every bed that goes through the machine.
Additional Measuring Devices
The integration of the roll cage calculator does a few things. First, it gives awareness to the infeed and press of the compression folding system. With additional sensors and a scale at the infeed, product weight and dimensions are taken and stored in the machine’s database for the incoming product. As the product is compressed, the tamp press is reading the force deflected back onto the press, which is then used to calculate the level of compression that product can handle.
Data-Driven Roll Cage Adjustments
Using the initial dimensions with the data collected during compression, the machine automatically adjusts its roll cage to the ideal dimensions for that product within a predetermined tolerance. The product then shuttles to the cage and is packaged accordingly. If for some reason the dimensions are off or the force-deflection is measuring outside of tolerance, the machine will automatically alert the operator that the product is faulty and it will not be packaged. This protects the machine from damage and ensures only quality product is packaged and shipped to customers.
Eases Operator Responsibility
When we leave the measurement and calculations to the machine, the operator’s job gets easier. No longer is it their responsibility to visually check if a bed seems out of spec, nor do they need to remember multiple recipe inputs or variances. This is all in the machine’s control. Now the operator can focus on keeping the machine fed and monitoring notifications; a simpler and less-demanding workload.
Added Functionality Brings New, Smaller Product Dimensions
This technology made advancements like the second roll cage possible. When we are monitoring the product’s actual dimensions and the responsiveness of the product in real-time, we’re able to push the product further safely. The second roll cage uses this technology to decrease the final package size by nearly half, giving manufacturers that produce all-foam beds a new option in packaging dimensions for their products.
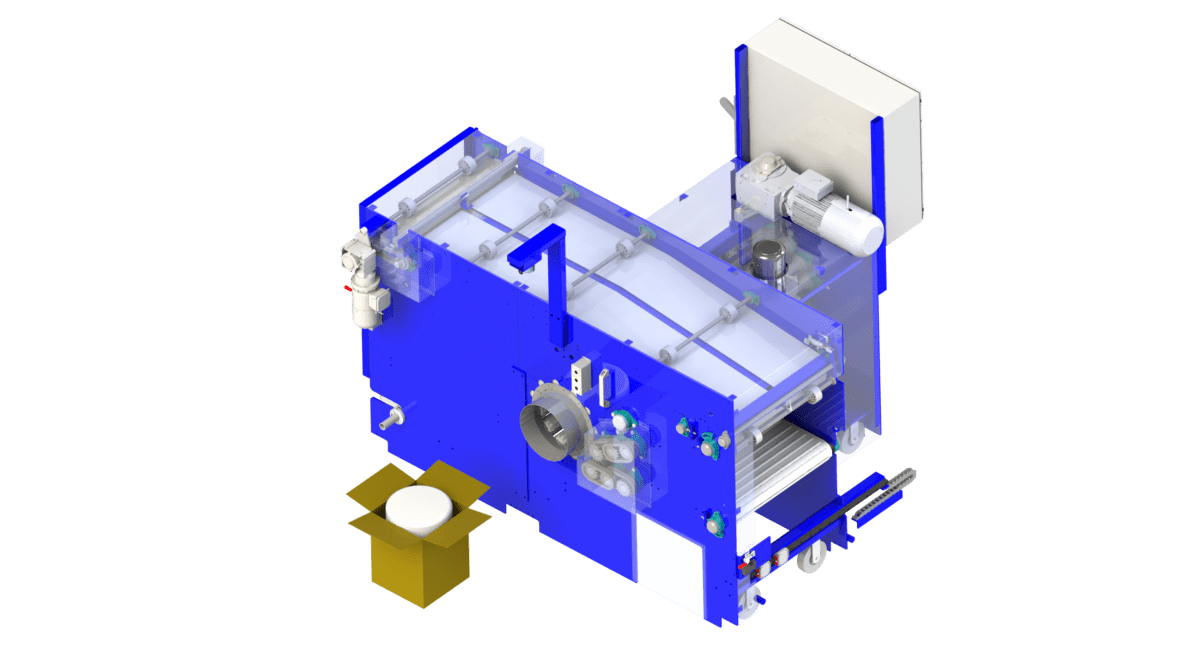
Learn more about the second roll cage here.
Ready to see the variable cage for mattress packaging in action? We’ll be showcasing the compression folding system with the new smart features at ISPA Expo, March 18-20th, 2020 in New Orleans at Booth 100. See how the machine packages beds right from the lamination section and how these smart features aid in the packaging process.